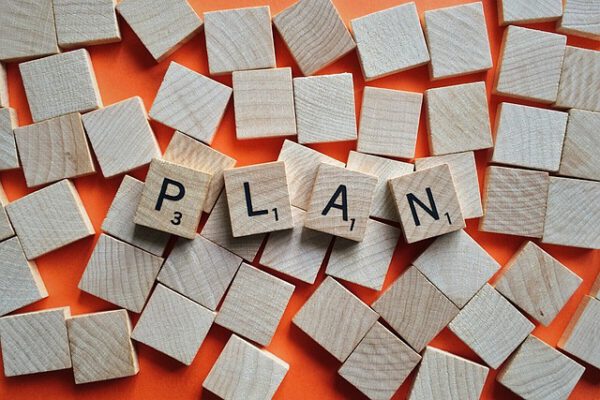
autor: Adrian Knapczyk
Bardzo często słyszymy, że jeden obraz jest wart tysiąca słów i tak właśnie jest, jeśli chodzi o mapowanie procesów produkcyjnych. Sam proces mapowania możemy zdefiniować jako graficzną architekturę procesową przedsiębiorstwa. Głównym celem mapowania jest pokazanie co się dzieje aktualnie w przedsiębiorstwie w chwili obecnej oraz co ma się dziać w przyszłości.
Metody optymalizacji produkcji
Graficzna forma przedstawienia procesów porządkuje etapy procesu, wskazuje realne przepływy, ale musi być również transparentna i czytelna. Takie uporządkowanie procesów daje możliwość skorzystania z klasycznych metod optymalizacji. Do takich metod możemy zaliczyć optymalizację sieciową:
- CPM (ang. Critical Path Method),
- CPM-COST (metoda CPM rozszerzona o analizę kosztową),
- PERT (ang. Program Evaluation and Review Technique),
- PERT-COST (metoda PERT rozszerzona o analizę kosztową).
Mapowanie procesów i metody optymalizacji – co nam to daje?
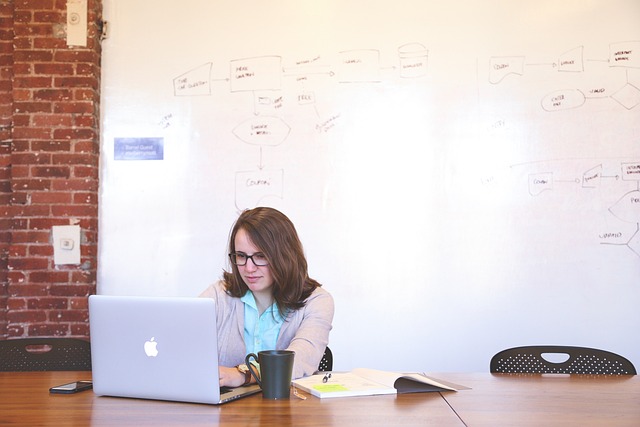
Dzięki zastosowaniu tych metod jesteśmy w stanie wskazać krytyczne punkty kontroli, miejsca procesu wpływające bezpośrednio na długość całości. Metody uwzględniające czynnik kosztowy dają możliwość oszacowania kosztu skrócenia procesu.
Może się okazać, że koszt skrócenia procesu, dzięki zastosowaniu np. nowej maszyny jest niewspółmierny do zysków skrócenia. Oprócz oczywistych zalet w postaci możliwości optymalizacji, mapowanie procesów może posłużyć w szkoleniu nowych pracowników. W początkowej fazie kariery w danym przedsiębiorstwie jest to doskonała ściąga służąca w zrozumieniu przebiegu produktu od surowca do produktu końcowego.
Popularne sposoby mapowania procesów
Najbardziej znanymi sposobami mapowania procesów są: diagram procesu, diagram przepływu, mapowanie strumienia wartości. Każda z tych metod zupełnie inaczej podchodzi do tematyki oraz ma inne przeznaczenie.
Business Process Model and Notation
Głównym sposobem graficznego przedstawienia procesów jest diagram przepływu (ang. Data Flow Diagram). W zależności od branży możemy używać różnych notacji do modelowania procesów. W inżynierii produkcji najbardziej przydatne jest modelowanie procesów biznesowych. Najczęściej wykorzystywaną notacją jest BPMN (ang. Business Process Model and Notation). Obecnie stosuje się już standard 2.0. Notacja sama w sobie dostarcza elementy graficzne (ikony oraz kształty), które są wykorzystywane do modelowania procesów biznesowych.
Plusem wykorzystania notacji BPMN 2.0 jest jej czytelność dla menedżerów, analityków biznesowych, programistów. Do tworzenia diagramów możemy użyć takich narzędzi jak: MS Office Visio, Flowcharter, Bizagi Process Modeler, ARIS Toolset, Adonis, Workflow Analyzer i wielu innych.
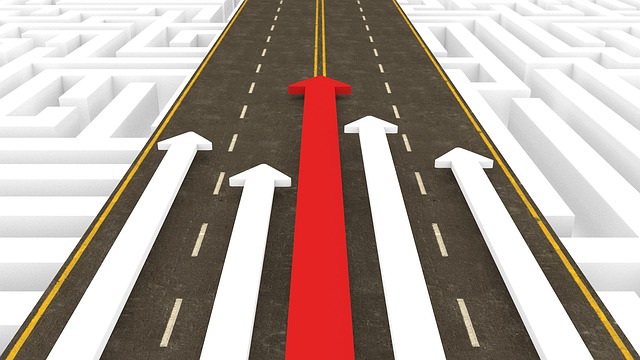
Jak zacząć mapowanie procesów?
Poprawne mapowanie procesów należy rozpocząć od identyfikowania głównych uczestników procesu, a dopiero w drugiej kolejności przejść do tworzenia szczegółowej mapy procesu. Identyfikację procesów możemy zrealizować dwoma metodami. Pierwsza z nich to metoda odgórna (top-down), w której to definiujemy ogólną działalność przedsiębiorstwa, jej cele i misje, a potem przechodzimy do uszczegóławiania poszczególnych fragmentów. Druga to metoda oddolna (bottom-up), która skupia się na czynnościach wykonywanych w przedsiębiorstwie, a potem na podstawie nich są opisywane procesy. Drugie podejście jest znacznie bardziej pracochłonne.
Mapowanie procesów – zalety
Do niewątpliwych zalet mapowania można zaliczyć:
- przejrzystość diagramu procesu,
- możliwość dalszej optymalizacji,
- łatwą interpretację,
- łatwą możliwość modyfikacji,
- łatwiejsze zarządzanie procesowe.
Podejście to jest jednak wymagające pod względem samego wdrożenia. Niezbędny jest zespół osób, który po pierwsze zna doskonale istniejące procesy w przedsiębiorstwie, a po drugie zna elementy notacji biznesowej BPMN 2.0. Diagramy takie można tworzyć na różnym poziomie uogólnienia. W ramach jednego dużego procesu, można tworzyć diagramy fragmentów procesów, ale za to o wyższym poziomie szczegółowości.