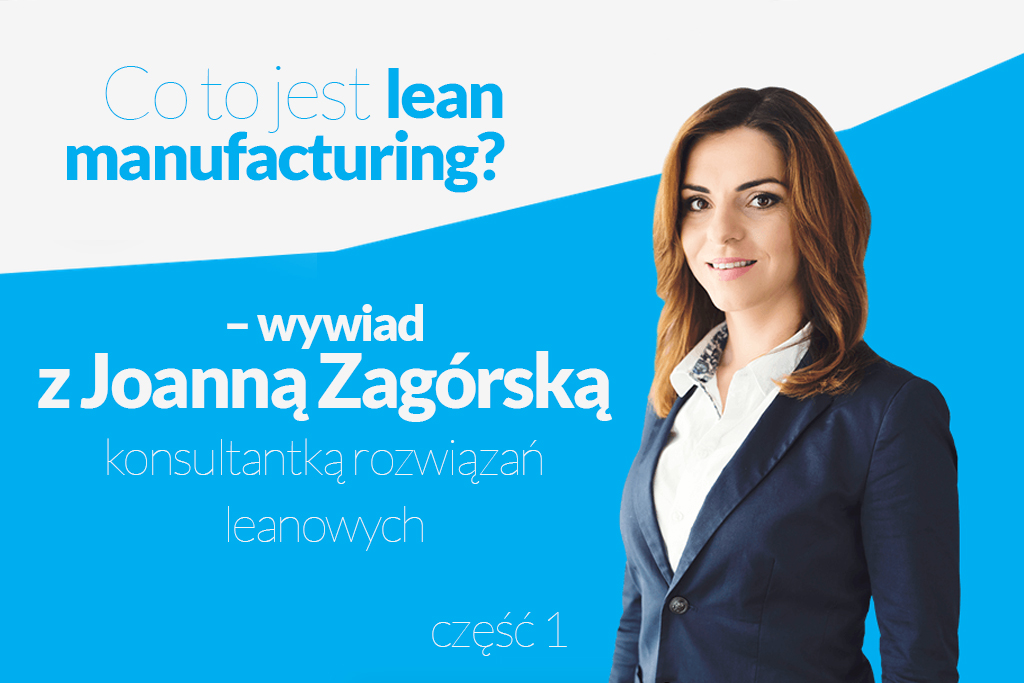
Jest wyjątkową postacią nie tylko dlatego, że wie co to jest lean manufacturing. Przyciąga do siebie swoją otwartością i widocznym od pierwszego kontaktu zaangażowaniem w projekt. Odwiedziła do tej pory ponad 50 krajów, a w 16 z nich uczyła się lub pracowała. Jest ekspertką strategii lean manufacturing, które z powodzeniem wprowadza w firmach na całym świecie. W przedsiębiorstwach, do których została zaproszona bada istniejące problemy, proponuje ich rozwiązanie i ostatecznie je wprowadza. Poza pełnym sukcesów życiem zawodowym prywatnie oddaje się licznym pasjom sportowym i samorozwojowi. Bez wahania podejmuje nowe wyzwania, znajdując odpowiedni balans w każdej strefie życia.
O tym jak wprowadzić równowagę w życiu zawodowym, po co w biznesie potrzebna jest konsultantka, oraz czym jest podejście lean manufacturing – co to jest i dlaczego warto poświęcić mu uwagę opowie nam ekspertka – Joanna Zagórska.
- Co to jest Lean manufacturing?
Poza definicją naukową powiedziałabym w skrócie, że to jest leń. Chodzi o to, żeby nie robić tego, czego nie trzeba. Przyglądamy się procesom i określamy co jest marnotrawstwem, a co jest wartością dodaną. Bardzo często ludzie zapominają, albo nie wiedzą, że wartość dodaną definiuje klient. To są wszystkie te czynności, za które chce on zapłacić i które są za pierwszym razem poprawnie wykonane. Czyli „klepanie”danych z Excela do innego formularza to na pewno jest marnotrawstwo, bo nic nie zmienia.
- Spośród tylu filozofii dlaczego akurat ta?
Gdy skończyłam studia, pojechałam do Anglii, żeby się nauczyć czegoś ciekawego. Jeden z naszych sąsiadów zajmował się lean manufacturing. Zaczął mi opowiadać, że w lean manufacturing chodzi o ciągła zmianę w ludziach i wzięcie odpowiedzialności za to czym się zajmują, żeby mogli decydować jakie zmiany są najlepsze. Wtedy intuicja podpowiedziała mi, że jest to interesujące i że to do nas dotrze dopiero w przyszłości. Wtedy dostałam się na dwuletni staż w firmie, która wyciągnęła się lean manufacturing z bankructwa. Lean to jest kultura pracy, to nie jest projekt, to nie tylko zestaw narzędzi, tylko cała filozofia. To jest bardziej holistyczne podejście do zarządzania firmą. To właśnie mnie najbardziej zaciekawiło – lean manufacturing jest dla ludzi.
Lean manufacturing to sposób zarządzania przedsiębiorstwem produkcyjnym, przy maksymalnym ograniczeniu wszelkiego marnotrawstwa i dostarczaniu klientowi produktów najwyższej jakości.
Lean manufacturing. Definicja
- Skąd pomysł, że lean manufacturing sprawdzi się wśród polskich przedsiębiorców?
Głównie dlatego, że w Polsce jest więcej do zrobienia. Na pewno chodzi o zmianę mentalności w firmie. Jeśli w Rosji się sprawdza, to dlaczego miałoby się u nas nie sprawdzić? Poza tym po tych jedenastu projektach byłam już trochę zmęczona podróżowaniem, więc wraz z córką stwierdziłyśmy, że osiądziemy i nie będziemy się już przeprowadzać.
- Czy w Polsce sprawdzają się narzędzia lean manufacturing? Czy przedsiębiorcy są chętni do zmiany swojej dotychczasowej filozofii?
Młodsze pokolenia są dużo bardziej świadome i szukają ciekawszych rozwiązań niż te peerelowskie, które mamy jeszcze niestety głęboko zakorzenione. Tamta kadra już powoli odchodzi i wchodzi nowy duch. Wydaje mi się, że dużo osób się szkoli i zauważa, że może nie wiedzieć wszystkiego. Tutaj chodzi też o to, żeby odpuścić nieco kontrolę i odwrócić hierarchię w firmie.
Najczęściej zarząd, czyli tzw. „góra” daleka jest od procesów produkcyjnych, gdyż jest zamknięta w gabinetach przed komputerami, a kiedyś przed papierowymi raportami. Chodzi o to, żeby wspierali, a nie rozkazywali, bo najczęściej na procesach najlepiej znają się ci ludzie, którzy codziennie z nimi pracują. Więc taką kadrę wysyła się do tzw. „GEMBA” (z japońskiego – the real place), czyli do tego miejsca, gdzie dzieją się procesy i za zadanie mają przebywać tam, pomagać i wspierać. Wtedy obserwują wszystko w czasie rzeczywistym. Czyli nie na podstawie starych raportów, tylko aktualnych danych.
Lean management to podejście do zarządzania całą organizacją (a nie tylko produkcją), którego podstawą jest nieustanne dążenie do doskonałości, a celem uzyskanie coraz lepszej efektywności pracowników.
Lean manufacturing a lean management
- Z jakimi problemami borykają się przedsiębiorcy, którzy zgłaszają się do Ciebie? Czy są one gdzieś opisane? Istnieje coś takiego jak np. książka “Co to jest lean manufacturing? – o problemach przedsiębiorców“
Każda firma uważa, że jest wyjątkowa i z pewnością tak jest, ale są pewne problemy, które można skategoryzować. Marnotrawstwa też się powtarzają. Obecnie mówi się, że to już nie osiem, a dziewięć marnotrawstw, które są w każdym procesie. Problemy różnią się w zależności od wielkości firmy. Zwłaszcza dla małych firm, które chcą urosnąć i wyjść z tzw. garażu problemem bardzo często jest brak standardów i procedur. Każdy pracownik robi jak uważa najlepiej. Chodzi o to, żeby zebrać tą najcenniejszą wiedzę od wszystkich pracowników i stworzyć jeden standard, który będzie dostarczał klientowi zawsze tę samą jakość i wartość. Bardzo często decyzje są opierane na podstawie „widzi mi się”, a nie na podstawie danych.
Marnotrawstwami, o których wspomniałam są np. źle zorganizowany transport, zbędne zapasy, nadprodukcja, błędy i defekty, zbędny ruch, a ostatnio doszło również obwinianie. Lean manufacturing zakłada, ze 90% błędów jest wynikiem złego procesu, a nie tego, że ludzie chcą je popełniać. Proces jest tak stworzony, że pozwala na popełnienie błędów i trzeba go zmienić w taki sposób, żeby się nie dało ich popełniać.
- Czy za każdym razem udaje się poprawić te problemy, z którymi zgłaszają się przedsiębiorcy?
Na pewno nie zawsze się udaje. Odpowiadając na pytanie co to jest lean manufacturing można powiedzieć, że jest to ciągłe usprawnianie i udoskonalanie. Często taki konsultant pokazuje co i jak zmienić, później co trzeba robić dalej, żeby tę zmianę utrzymać, ale co z tym zrobi firma to już od nich zależy. W dużych korporacjach pojawiają się problemy, które się wzajemnie wykluczają. Często ludzie pracują w określony sposób, a później przychodzi jakaś zmiana, restrukturyzacja i wszystko bierze w łeb. Najważniejsze jest, żeby zachęcić ludzi do zmiany i dać im odczuć, że te zmiany są dla nich i że są dobre. Ale, czy zarząd będzie dalej tego pilnował, to już od nich zależy. Jeżeli ludzie nie będą wspierani, to też odpuszczą, bo po co się wysilać.
Zarząd powinien dopilnować ludzi i wspierać, a także dawać czas na to, żeby mogli oni dalej usprawniać proces. No i też nagradzać, doceniać, a tego często brakuje. Leanowe przywództwo to właśnie sposób w jaki kierownictwo podchodzi do ludzi i tych zmian.
- Co poza samą filozofią usprawnia działanie przedsiębiorstwa? Z jakich narzędzi korzystasz, albo które polecasz?
Narzędzia lean manufacturing to cały wachlarz przeróżnych rozwiązań. Chodzi o to, żeby je mądrze dopasować do problemów, które się w danej firmie wydarzają. Bardzo ważna jest komunikacja i odprawy. Od tego powinno się zacząć. Ludzie powinni się spotykać, rozmawiać na temat problemów, oraz o swojej pracy, czyli kto się czym zajmuje. Kolejnym narzędziem jest zarządzanie wizualne, czyli wszystko ma być widoczne, a nie pochowane w folderach podfolderów gdzieś w komputerach. Robi się tablice wizualne i przy pracownikach odbywają się krótkie 5-10 minutowe odprawy, ale codziennie. To wystarcza ludziom, bo wtedy wszystkie problemy są „wymiatane spod dywanu”.
Pracownicy są zwykle przytłoczeni ilością zadań dodatkowych, które mogą być nierozwiązane i zalegają często ukrywane, bo nie ma na nie czasu. Trzeba powyciągać takie rzeczy z szafy, żeby się „odkopać”. To bardzo wpływa na kulturę pracy. Pierwszą rzeczą jaką widać w leanowych firmach jest spokój. Nie ma chaosu, każdy wie czym się zajmuje, co robi, jak mu poszedł ostatni dzień. Poza tym jest masa narzędzi, które do danego procesu można dopasować.
- Czy aplikacja do zarządzania produkcją jest jednym z narzędzi, które wpisują się w filozofię lean manufacturing?
Jak najbardziej. Zbieranie danych i to w czasie rzeczywistym umożliwia podejmowanie decyzji na ich podstawie. Aplikacja powinna być na tyle prosta i łatwa w obsłudze, żeby można było te dane zwizualizować zamiast spisywać je na kartce, co działo się przez lata m. in. w Toyocie. Przejrzystość danych pomaga mieć kontrolę nad procesami, których one dotyczą. Dzięki temu można podejmować lepsze decyzje. Chodzi o to, żeby być proaktywnym. Mając bieżące dane widać pewne trendy, więc można od razu reagować.
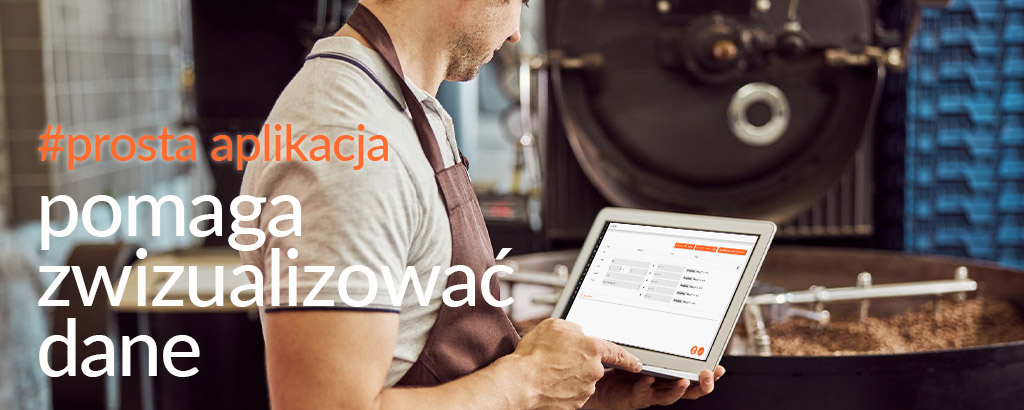
- W niektórych szkoleniach z zarządzania produkcją szczególna wagę przykłada się do zmniejszenia ilości spotkań. Te meetingi są traktowane jako strata czasu. Im mniej spotkań tym lepiej. Dlaczego w lean manufacturing jest inaczej?
Dobrze jest robić codziennie krótkie, kilkuminutowe odprawy. Niejednokrotnie wyciągaliśmy ludzi z godzinnych odpraw w salach konferencyjnych, gdzie mieli stosy kartek i każdy coś prezentował. Zmieniliśmy miejsce i charakter spotkań. Wyciągnęliśmy ich do tak zwanej GEMBY, czyli na produkcję. Tam przed tablicą wizualną odprawy były bardziej konkretne i krótsze. Ilość informacji, jaką można przekazać przy takiej tablicy wizualnej na produkcji jest dużo większa niż w sali konferencyjnej. Taki sposób odprawy bardziej przemawia do ludzi, ponieważ odbywają się na stojąco. Nikt się zatem specjalnie nie rozgaduje, więc podawane są tylko konkrety. Dodatkowo, wizualnie przekazane informacje bardziej przemawiają do ludzi, ponieważ w taki sposób się i pokazuje, i mówi. To dociera także do kinestetyków, ponieważ jest interakcja przy takiej tablicy. Takie spotkania są inne – krótkie i treściwe.
- Co to jest mapowanie? Wygląda to dość podobnie do wdrażania nowych procesów w aplikacji do zarządzania produkcją. Do czego służy mapowanie?
Mapowanie strumienia wartości w całej firmie to określenie którędy przepływa wartość firmy. Mapowanie procesów, to analiza elementów, które się w tym strumieniu zawierają. Chodzi o to, żeby wziąć kartkę, zebrać ludzi i narysować czynność po czynności wszystkie zadania, które wykonują w danym procesie. Następnie analizuje się, czy jest to marnotrawstwo, czy wartość dodana. Wypisuje się dane, czyli czas, zapasy, jakie się ma na określonym etapie. Wtedy powstaje rysunek procesu, który w takiej formie można zrozumieć w 10 minut. Jest to łatwiejsze dla pracowników i trwa zdecydowanie krócej niż kilkugodzinny wykład podczas konferencji.
Mapowanie to pierwszy etap do zrozumienia procesu. Bardzo często pewne etapy produkcji przechodzą przez różne działy w firmie. Niektórzy w jednym dziale nie mają pojęcia co się dzieje w drugim. Wtedy powstaje bardzo dużo marnotrawstw, bo często powielane są pewne czynności. Dopiero wówczas, gdy się zbierze wszystkich ludzi z różnych etapów tego procesu i razem z nimi to narysuje, to pojawiają się takie refleksje „wow, to wy to robicie? Przecież my to robimy”. Dzięki temu poprawiamy też komunikację. Mapowanie pozwala przyjrzeć się dokładnie jak wygląda proces. Wtedy łatwo zobaczyć co jest marnotrawstwem, a co jest wartością. Są tzw. „nawrotki” w procesie, czasem niepotrzebne, całość idzie do przodu, a ludzie zauważają, że jest brak danych i dokument wraca do innego działu. Takie rzeczy się prostuje i usprawnia, co oszczędza czas. Ludzie nie lubią robić bezsensownych rzeczy. Często o tym wiedzą, ale nikt nie daje im możliwości, żeby o tym mówili.
- Gdyby strategia lean manufacturing miała być programem, to jakie elementy powinna mieć w sobie? Czyli lean manufacturing – definicja dobrego programu do zarządzania.
Na pewno ludzie i komunikacja, procesy i ciągłe udoskonalanie. To są podstawowe składowe programu. Zaczynając od ludzi – chodzi o to, by dobrać właściwych ludzi na stanowisko. Do tego też jest narzędzie, np. matryca kompetencji, która sprawdza co ci ludzie potrafią, czego nie i w którym kierunku chcą się rozwijać. Program powinien zatem umożliwiać ludziom sprawną pracę na określonym stanowisku, gdzie zostało jasno określone co mają robić, jak mają to zrobić i w jakim czasie.
Komunikacja – drugi element, czyli odprawy i przepływ informacji ma być jak najszybszy. Program powinien prezentować od razu na profilach pracowniczych jakie zmiany zostały wprowadzone do systemu przez zwierzchników. W przypadku procesów – muszą się one opierać na danych. Każdy proces trzeba mapować i usprawniać. Wymaga to bardzo dużo czasu, żeby mapowanie było wykonane prawidłowo. Zwłaszcza, że ludzie przychodzą do pracy i mają swoje regularne zajęcia. Program zatem powinien być na tyle intuicyjny i prosty w obsłudze, żeby nie komplikował pracy, a usprawniał ją.
Na końcu ciągłe udoskonalenie. Jak już wdrożymy te procesy, to ich nie zostawiamy, tylko nad nimi nieustannie pracujemy. Bo bez udoskonalania nam się „rozjadą”. To jest naturalne. Jedyną stałą jest zmiana.
- W jaki sposób aplikacja do zarządzania produkcją FACTORY plus realizuje założenia lean manufacturing?
Przede wszystkim zbieranie aktualnych danych. Organizacja i kontrola zapasów. W leanie chodzi o kontrolę procesów i to w czasie rzeczywistym. Jeśli te dane są automatycznie zbierane i jeszcze wizualizowane, czyli każdy może spojrzeć na monitor i zobaczyć jak ten proces przebiega, to jest to największa zaleta.
Sprawdź jak działa aplikacja do zarządzania produkcją FACTORY plus w wersji darmowej
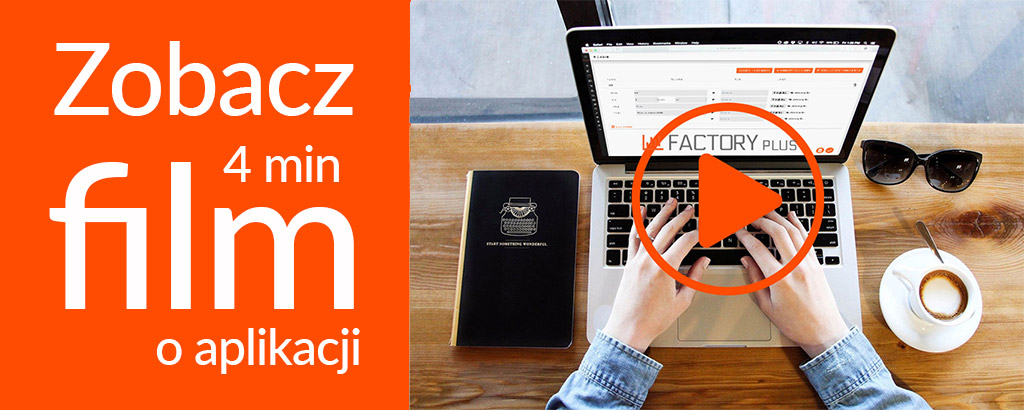
W drugiej części wywiadu Joanna Zagórska opowie m. in. o organizacji pracy w fabryce BMW, oporach pracowników wobec wprowadzanych zmian oraz przedstawi co dokładnie powinien zrobić pracodawca, by w swojej firmie skutecznie dokonywać pozytywnych zmian. Link do drugiej części wywiadu dostępny jest tutaj.