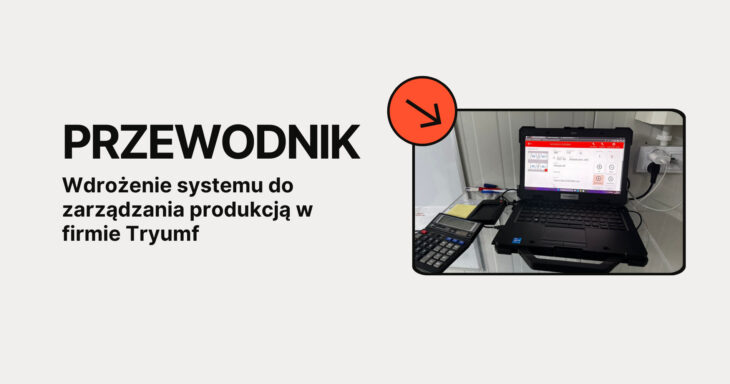
1. Wdrożenie systemu to Twoja droga do usprawnienia produkcji
Każde wdrożenie programu do zarządzania produkcją to nie tylko techniczne rozwiązanie, ale strategiczny proces, który ma na celu poprawę funkcjonowania całej firmy.
Jak przebiega proces wdrożenia programu do zarządzania produkcją? Wprowadzenie nowego systemu często budzi pytania: „Czy to jest odpowiedni moment?”, „Ile trwa proces wdrożenia aplikacji?” i „Czy wdrożenie jest kosztowne?”. Na te oraz inne wątpliwości odpowiemy, opierając się na doświadczeniach firmy Tryumf, która przeszła przez wszystkie etapy wdrożenia – od pilotażu, przez zrozumienie oczekiwań, aż po ciągły rozwój systemu.
Gotowy na podróż przez kolejne etapy wdrożenia? Omówimy każdy z nich krok po kroku, pokazując, jak przekształcić wdrożenie w sukces. Zainspiruj się przykładami z firmy Tryumf i sprawdź, jak możesz wdrożyć oprogramowanie do zarządzania produkcją już dziś.
1.1 Problemy do pokonania: Co system zarządzania produkcją może poprawić?
W każdej firmie, zanim wdrożysz program do zarządzania produkcją, warto zadać sobie podstawowe pytanie: „Co chcę osiągnąć?”. W firmie Tryumf kluczem do sukcesu było dokładne zdefiniowanie problemów, które system miał rozwiązać. Bez tego wprowadzenie systemu mogłoby przypominać strzelanie na oślep – dużo wysiłku, mało efektów.
Identyfikacja kluczowych wyzwań – problemy z którymi borykała się firma Tryumf
- Ręczna rejestracja danych
Dla Tryumfu jednym z głównych problemów była ręczna rejestracja danych, która prowadziła do chaosu, błędów i marnowania czasu. Wyobraź sobie, że masz setki zleceń dziennie, a każde pracownik musi wpisać na kartkę, a później przenieść do systemu – brzmi jak koszmar, prawda?
- Niestandardowa produkcja
Kolejnym wyzwaniem była niestandardowa produkcja. Każdy produkt – od statuetek po laser cutting – wymagał innego podejścia z uwagi na szeroką gamę materiałów i skomplikowane procesy wytwórcze, co utrudniało standaryzację procesów i porównywanie wyników. Standaryzacja i porównywanie wyników było prawie niemożliwe, ponieważ nawet produkty z tej samej serii różniły się szczegółami, takimi jak technologia druku czy wzornictwo.
- Przejrzystość kosztów produkcji
Wyobraź sobie, że planujesz budżet na produkcję, ale nie wiesz, ile naprawdę kosztuje wytworzenie poszczególnych produktów. W Tryumfie często korzystano z zaokrąglonych średnich czasów pracy i uproszczonych wyliczeń materiałowych, co prowadziło do niedokładnych analiz i problemów z wyceną.
- Niska jakość danych
Dane wprowadzane na kartach pracy były nieprecyzyjne, często zaokrąglone lub dopasowywane “na oko”. To prowadziło do niedokładnych analiz wydajności oraz kosztów. W efekcie firma nie mogła polegać na posiadanych danych przy podejmowaniu kluczowych decyzji.
- Trudności w standaryzacji i planowaniu
Brak systematycznego podejścia do rejestrowania procesów skutecznie utrudniał planowanie produkcji. Weźmy na przykład produkcję statuetek – różnice między projektami były tak ogromne, że określenie realnych norm czasu czy zasobów graniczyło z cudem. W efekcie firma zmagała się z przestojami i problemami w harmonogramowaniu, co potrafiło wywrócić cały plan do góry nogami.
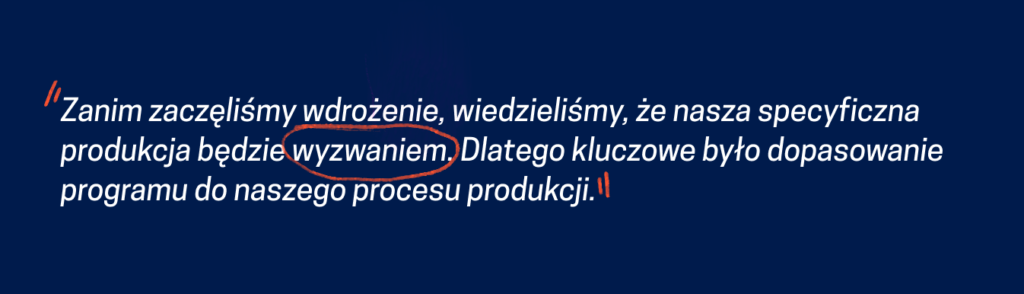
1.2 Warsztat zerowy dla produkcji: solidny fundament przed wdrożeniem
Wdrożenie programu do zarządzania produkcją to nie tylko wprowadzenie technologii – to przede wszystkim ludzie i procesy, które trzeba odpowiednio przygotować. Dlatego warsztat zerowy to kluczowy etap, który zwiększa szanse na sukces. To moment, kiedy razem z klientem siadamy do stołu, analizujemy procesy, wyłapujemy najważniejsze potrzeby i tworzymy solidny fundament pod efektywne działanie systemu.
Jak to wyglądało w praktyce?
Warsztat zerowy w Tryumfie to była okazja, żeby prześwietlić cały proces produkcji od A do Z.
- Burza mózgów z zespołem – każdy dział zgłaszał swoje problemy i potrzeby. Dzięki temu uwzględniono różnorodne perspektywy.
- Analiza danych – porównano, jakie procesy są najtrudniejsze do monitorowania, a które można zoptymalizować.
- Mapowanie procesów biznesowych w firmie – dokładne prześledzenie każdego etapu pracy pozwoliło zidentyfikować kluczowe punkty wymagające usprawnień. To nie było tylko siedzenie nad papierami, ale konkretna praca nad dopasowaniem systemu do ich realiów.
Na przykład:
- Przy statuetkach Prestige musieliśmy uwzględnić takie niestandardowe operacje, jak precyzyjny druk i dodatkowe wykończenia.
- Połączenie systemów też przeszło dokładną weryfikację, żeby dane mogły płynnie i bezbłędnie przepływać między ERP a nowym oprogramowaniem.
- Niektóre procesy wymagały ręcznej rejestracji.
Takie kwestie lepiej rozwiązać na etapie planowania, niż mierzyć się z nimi już po wdrożeniu.
Dowiedz się więcej o mapowaniu procesów optymalizacji produkcji.
Priorytetyzacja problemów – wybrano najważniejsze wyzwania, które wymagały natychmiastowego rozwiązania. W Tryumfie były to:
- Ręczne wprowadzanie danych.
- Niska jakość informacji.
- Trudności z monitorowaniem procesów w czasie rzeczywistym.
Dlaczego to ważne?
Definiowanie kluczowych problemów oraz mapowanie procesów biznesowych w firmie pozwala uniknąć rozczarowań i niepotrzebnych kosztów. Zamiast kupować system, który rozwiązuje problemy, których nie masz, inwestujesz w narzędzie, które rzeczywiście poprawia efektywność. W przypadku Tryumfu efektem było między innymi:
- Minimalizacja ryzyka błędów – lepiej zaplanowane wdrożenie to mniej niespodzianek w późniejszych etapach.
- Oszczędność czasu – zamiast „gaszenia pożarów”, można od razu skupić się na wdrażaniu systemu.
- Precyzyjne dostosowanie – każdy proces jest dopasowany do specyfiki klienta, dzięki czemu system działa płynnie od pierwszego dnia.
Jeśli chcesz, aby Twój program do zarządzania produkcją rozwiązywał realne problemy, zacznij od ich dokładnego zdefiniowania i mapowania procesów biznesowych w firmie.
1.3 Proces wdrożenia pod klucz – dobre dopasowanie do potrzeb firmy to krok do sukcesu
Dopasowanie systemu do skali i specyfiki firmy Tryumf
Tryumf wiedział, że dostosowanie programu do procesu produkcji to podstawa. Zamiast dopasowywać firmę do programu, dostosowano program do firmy. Na przykład: funkcje rejestracji danych zostały tak skonfigurowane, aby uwzględniały różnice między procesami, takimi jak statuetki czy odlewy.
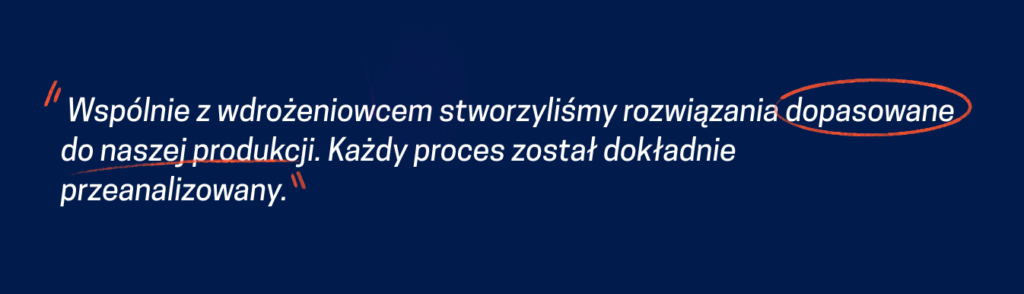
Wdrożenie programu do zarządzania produkcją odbyło się etapami, co okazało się kluczem do sukcesu. Jeśli prowadzisz firmę z niestandardową produkcją, na pewno wiesz, że dopasowanie systemu do specyficznych potrzeb może być wyzwaniem. Tryumf pokazał, że dzięki dobrej strategii i współpracy z doświadczonym wdrożeniowcem można to zrobić bez zbędnych komplikacji.
Jak wyglądał proces wdrożenia programu w praktyce?
Pilotaż zamiast chaosu
Wyobraź sobie, że próbujesz od razu wdrożyć nowy system w całej firmie. Brzmi jak przepis na bałagan, prawda? Zanim system został wdrożony na pełną skalę, przeprowadzono testy funkcjonalne i pilotażowe (proof of concept). Dzięki temu każda funkcja była dokładnie przetestowana, a ewentualne błędy można było wychwycić.
W tym czasie dane były rejestrowane zarówno w sposób tradycyjny (na kartkach), jak i w systemie, co pozwalało na walidację wyników i upewnienie się, że wszystko działa poprawnie. Takie podejście umożliwiło uniknięcie globalnych problemów, które mogłyby się pojawić przy wdrażaniu systemu na całą firmę.
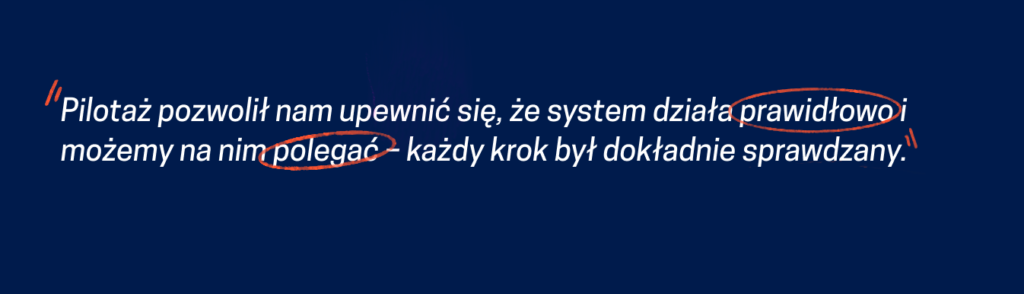
Ważne elementy pilotażu:
- Analiza procesów produkcyjnych przed wdrożeniem – Każdy etap produkcji został dokładnie przeanalizowany, by zrozumieć, jakie funkcje systemu będą kluczowe.
- Testy równoległe – Dane rejestrowano jednocześnie w sposób tradycyjny (kartki) i w systemie. Pozwoliło to na walidację wyników i upewnienie się, że wszystko działa poprawnie.
- Eliminacja błędów na bieżąco – Problemy wykrywane w czasie testów były natychmiast rozwiązywane, co pozwoliło uniknąć chaosu przy wdrożeniu na większą skalę.
Kluczowe elementy procesu wdrożenia programu do zarządzania produkcją:
- Doświadczony zespół wdrożeniowy – Osoba odpowiedzialna za wdrożenie była obecna na miejscu, co pozwoliło na szybkie reagowanie na potrzeby i pytania zespołu.
- Pełne wsparcie na każdym etapie – Problemy rozwiązywano zarówno zdalnie, jak i na miejscu, co przyspieszyło cały proces.
- Dostosowanie do specyficznych wymagań – Wdrożeniowiec doskonale rozumiał procesy w firmie i wspierał ich przekształcenie w funkcje systemu.
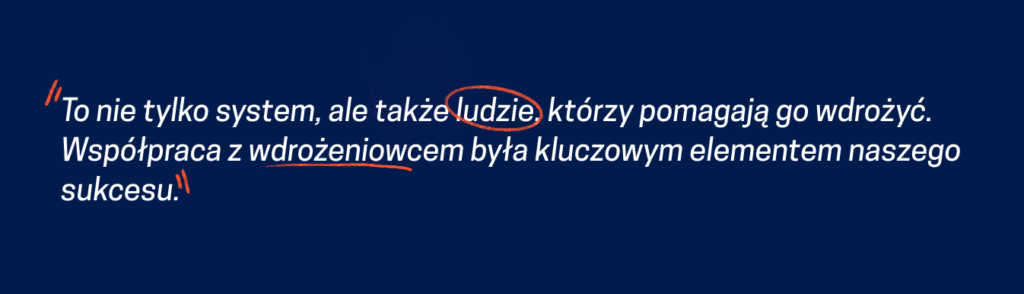
Jakie firma Tryumf miała założenia dotyczące wdrożenia?
Firma Tryumf wiedziała, że potrzebuje systemu, który rozwiąże problemy z ręczną rejestracją danych i pozwoli zapanować nad specyfiką ich produkcji. Kluczowe były:
- Konieczność integracji.
- Eliminacja ręcznego wprowadzenia danych.
- Wsparcie pracowników podczas wdrażania nowego systemu.
- Uwzględnienie specyfiki produkcji.
- Możliwość tworzenia dokładniejszych wycen.
- Stopniowe wdrożenie pilotażowe.
- Dokładność danych liczbowych na potrzeby analiz.
Jak rozwiązaliśmy problemy firmy Tryumf?
Po analizie wyzwań, z którymi zmagała się firma Tryumf oraz zapoznaniu się z potrzebami firmy, nasz zespół zaproponował konkretne rozwiązania, które nie tylko odpowiadały na ich potrzeby, ale także znacząco usprawniły procesy produkcyjne. Zamiast gotowych schematów, postawiliśmy na system dopasowany do ich specyfiki. Oto jak to zrobiliśmy:
1. Automatyzacja zamiast chaosu
Zamiast ręcznego przepisywania danych, wdrożyliśmy system rejestracji czasu pracy i zleceń z logowaniem za pomocą czytników kart RFID. Automatyczne zapisywanie danych wyeliminowało błędy i oszczędziło mnóstwo czasu.
2. Integracja systemów
Połączyliśmy nowy system z ERP, którego firma już używała. Dzięki temu wszystkie dane – od produkcji po magazyn i koszty – znalazły się w jednym miejscu. Co najważniejsze, zgromadzone dane nie zostały zgubione, a ich pełna integracja znacznie ułatwiła zarządzanie i planowanie, zapewniając płynność w codziennej pracy. Dodatkowo, stopniowe uruchamianie funkcjonalności pozwoliło na testowanie i wdrażanie kluczowych elementów systemu, minimalizując ryzyko błędów i zwiększając efektywność procesu.
3. Porządek w procesach
Zaproponowaliśmy ujednolicenie nazw produktów, operacji i narzędzi, co pozwoliło na lepszą organizację i porównywanie wyników. Chaos w danych? Zniknął raz na zawsze.
4. Stopniowe wdrożenie
Zaleciliśmy rozpoczęcie od jednego działu – laser cutting – jako pilotaż. Dzięki temu firma mogła przetestować system, poprawić niedociągnięcia i dopiero wtedy wdrożyć go na większą skalę.
5. Intuicyjność dla pracowników
Stworzyliśmy system, który był prosty i szybki w obsłudze. Dzięki temu pracownicy łatwo się go nauczyli, a my zapewniliśmy wsparcie techniczne na każdym etapie wdrożenia.
6. Przejrzystość na każdym etapie
Dzięki naszemu rozwiązaniu pracownicy zyskali pełną widoczność nad etapami produkcji, a kierownicy mogli łatwo monitorować wyniki i wydajność. To ułatwiło planowanie i wprowadziło większą kontrolę.
7. Szybsze wyceny
System umożliwił szybkie filtrowanie danych, co znacząco przyspieszyło wyceny – zadania, które wcześniej zajmowały godziny, teraz trwały minuty.
8. Szkolenia i liderzy
W ramach wdrożenia firma Tryumf wskazała liderów wśród pracowników, którzy pomogli reszcie zespołu w adaptacji do nowego systemu. Wspólnie pokazaliśmy, jak nowe narzędzia ułatwiają codzienną pracę.
9. System szyty na miarę
Uwzględniliśmy specyfikę niestandardowej produkcji Tryumfu, wprowadzając funkcje dedykowane pod ich potrzeby – od niestandardowych operacji po prace dodatkowe.
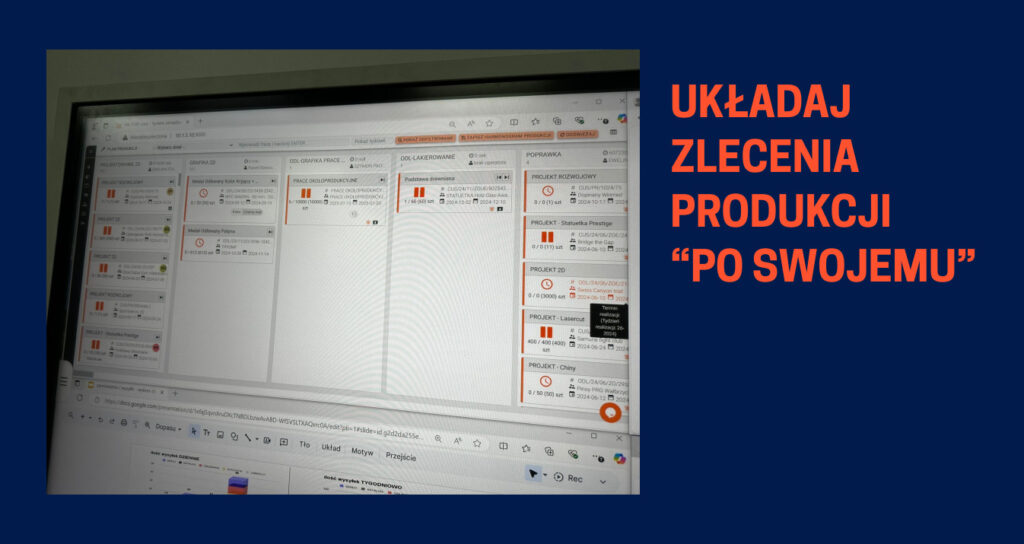
Ciągły rozwój w praktyce
Wdrożenie systemu w Tryumf to proces ciągły – nawet po roku od rozpoczęcia firma nadal dostosowuje go do nowych potrzeb, takich jak wprowadzenie nowych produktów czy modyfikacje procesów.
Kluczowym elementem było również monitorowanie postępów i rozwiązywanie błędów na bieżąco.
Z czasem pracownicy zgłaszali swoje uwagi. Niektórzy sugerowali, jak usprawnić rejestrowanie danych lub uprościć pewne operacje. Takie wskazówki były na bieżąco analizowane i gdzie to było możliwe wdrażane.
Chcesz zobaczyć, jak taki proces może wyglądać u Ciebie? Skontaktuj się z nami – pokażemy Ci, jak przebiega proces wdrożenia programu do
2. Najczęstsze obawy przed wdrożeniem systemu produkcyjnego
Wdrożenie systemu to nie tylko instalacja programu – to zmiana, która dotyka każdego w Twojej firmie, od zarządu po pracowników produkcji. Ważne jest, by zrozumieć, czego ludzie w firmie oczekują, a czego się obawiają.
W tej części przyjrzymy się najczęstszym obawom, jakie mogą towarzyszyć wdrożeniu systemu i pokażemy, jak je rozwiać. Na przykładzie firmy Tryumf opowiemy o ich procesie poszukiwania rozwiązania oraz o tym, co przesądziło o wyborze FACTORY plus.
Jak wyglądały poszukiwania firmy Tryumf systemu do zarządzania produkcją?
Firma Tryumf szukała rozwiązania, które faktycznie rozwiąże ich problemy produkcyjne, a przy okazji idealnie dopasuje się do ich potrzeb. Kluczowe było, żeby nowy system zgrał się z już istniejącym ERP, bo przecież nikt nie chce zaczynać wszystkiego od zera.
Szukali narzędzia, które nie tylko ma uniwersalne funkcje, ale też pozwala na personalizację – żeby w razie potrzeby można było dostosować je do specyficznych procesów produkcyjnych. Dopasowanie systemu do skali i specyfiki firmy było dla nich priorytetem, bo każdy proces wymagał uwzględnienia unikalnych cech ich działalności.
System musiał być też na tyle prosty w obsłudze, żeby pracownicy szybko się go nauczyli i nie czuli się przytłoczeni nową technologią. Wszystko to sprawiło, że wybór padł na rozwiązanie z intuicyjnym interfejsem i możliwością stałego wsparcia technicznego – bo nikt nie chce zostać z problemami sam.
Jakie były obawy firmy przed wdrożeniem systemu?
Przed wdrożeniem systemu w Tryumfie było trochę nerwowo. Największą obawą było, czy system w ogóle sprawdzi się przy tak niestandardowej produkcji. Jak ogarnąć tyle różnych procesów, skoro dotychczasowe systemy ledwo dawały radę? Do tego dochodziła kwestia integracji z ERP – co, jeśli coś się nie zgra i cała produkcja stanie w miejscu?
Były też obawy o ludzi. Czy pracownicy będą chcieli klikać w system? Czy ci mniej techniczni w ogóle dadzą radę? Pojawiały się pytania, czy te wszystkie zmiany nie spotkają się z buntem albo brakiem zrozumienia. No i wreszcie – czy wdrożenie nie pochłonie za dużo czasu i energii, zamiast faktycznie przynieść korzyści.
❓ Czy wdrożenie jest kosztowne i czasochłonne?
To pytanie pojawia się prawie zawsze, gdy mowa o wdrożeniu programu do zarządzania produkcją. Jasne, wdrożenie wymaga inwestycji – zarówno pieniędzy, jak i czasu. Ale doświadczenie firmy Tryumf pokazuje, że te wydatki są niczym w porównaniu do strat, które mogą wynikać z nieefektywności czy błędów w procesach produkcyjnych.
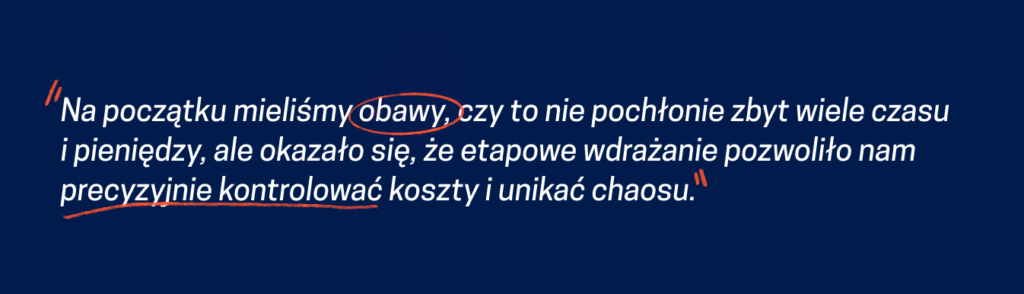
❓ Brak możliwości skonfigurowania programu pod nasz proces produkcyjny?
Firmy z niestandardową produkcją często zastanawiają się, czy program da się dopasować do ich specyficznych potrzeb. W Tryumfie na początku też były takie obawy – czy system faktycznie ogarnie ich różnorodne procesy? Kluczem okazała się ścisła współpraca z wdrożeniowcem. Dzięki temu udało się stworzyć rozwiązanie idealnie skrojone pod ich produkcję.
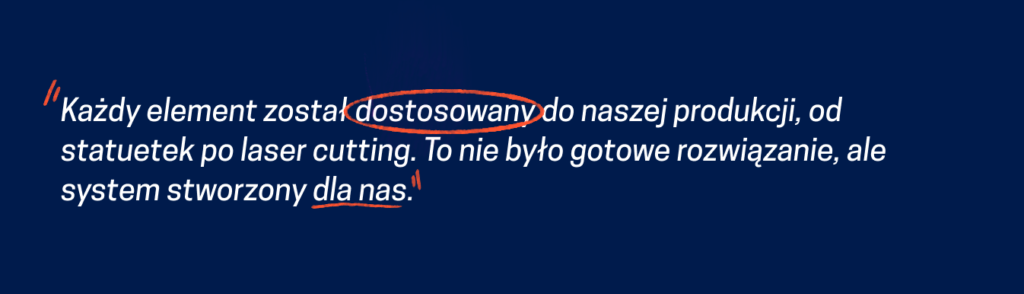
Indywidualne podejście sprawiło, że program nie tylko ułatwił codzienną pracę, ale stał się też narzędziem kluczowym do optymalizacji procesów. Dzięki temu firma mogła wprowadzać usprawnienia tam, gdzie wcześniej panował chaos, i skupić się na tym, co robią najlepiej – tworzeniu wyjątkowych produktów.
❓Czy jesteśmy za mali na wdrożenie?
Małe firmy często zastanawiają się, czy warto inwestować w system do zarządzania produkcją. Argumentem jest „jesteśmy za mali, możemy poczekać”.
Jednak, firma Tryumf dowiodła, że już w początkowej fazie wdrożenie przyniosło zauważalne korzyści, takie jak:
- Lepsza kontrola nad procesami produkcyjnymi – firma zyskała pełny wgląd w realizowane zlecenia i czas pracy.
- Oszczędność czasu administracji – eliminacja ręcznego wpisywania danych przełożyła się na redukcję kosztów osobowych.
- Podniesienie jakości danych – wprowadzenie systemu pomogło unikać błędów i chaosu w procesach.
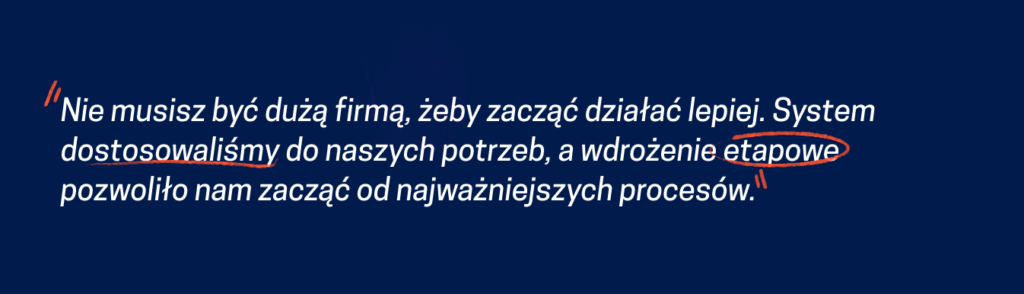
❓Kto przeprowadzi wdrożenie i ile trwa proces wdrożenia aplikacji?
W firmie Tryumf wdrożenie było prowadzone przez naszego wdrożeniowca – Piotra Laskowskiego, który dobrze znał specyfikę produkcji. Dzięki jego doświadczeniu i opiece w czasie wdrożenia, każdy krok był precyzyjnie zaplanowany, a wszystkie problemy rozwiązywano na bieżąco. Jak długo trwał ten proces? Wdrożenie jednego obszaru, obejmujące instalację infrastruktury, skonfigurowanie kont pracowników oraz dodanie maszyn i produktów do systemu, zajęło około tygodnia, a pełne wdrożenie systemu było rozłożone na etapy, aby dostosować go do potrzeb firmy.
3. Jak skutecznie przejść przez opór i adaptację pracowników podczas wdrożenia systemu?
Każda zmiana w firmie – zwłaszcza tak znacząca, jak wdrożenie nowego systemu – spotyka się z różnymi reakcjami pracowników. Od entuzjazmu po sceptycyzm, od ciekawości po otwarty sprzeciw. To naturalna część procesu, która może jednak stać się pierwszym krokiem do sukcesu, jeśli podejdzie się do niej w sposób przemyślany i konsekwentny.
Czy opór jest nieunikniony? Jak zbudować zaangażowanie w zespole? Jakie kroki warto podjąć, aby proces adaptacji przebiegł sprawnie? Jak szkolenia pracowników, budowanie świadomości i zaangażowania mogą wpłynąć na płynność tego procesu? Przyjrzyjmy się tym zagadnieniom bliżej!
3.1 Opór pracowników – case study firmy Tryumf
Początkowy opór wobec zmian jest naturalnym zjawiskiem w każdej organizacji. W firmie Tryumf wdrożenie systemu FACTORY plus spotkało się z różnymi reakcjami pracowników, od ciekawości, przez obawy, aż po otwarty bunt. Jednym z wyzwań było niedostateczne zaangażowanie zespołu.
Kluczem do sukcesu było skuteczne utworzenie zespołu wdrożeniowego po stronie klienta, który będzie wspierał proces adaptacji oraz budowanie świadomości i zaangażowania wśród całej załogi.
Problemy i wyzwania adaptacji pracowników
Początkowe reakcje były mieszane. „To co, teraz każdy nasz ruch będzie monitorowany?” – takie pytania padały najczęściej. Niektórzy pracownicy zareagowali z niepokojem, bo nowe narzędzie oznaczało koniec luźniejszego podejścia do ewidencji pracy. Ludzie często po prostu zastanawiali się, jak zmiany wpłyną na ich codzienną pracę.
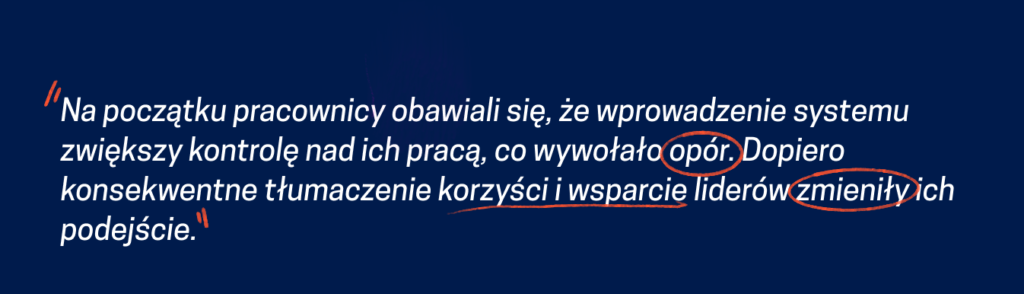
Problemy i wyzwania w trakcie wdrożenia
Pierwsze dni były trudne. Zdarzało się, że ktoś zapominał „kliknąć” w systemie, a liderzy zespołów musieli biegać po hali, przypominając o nowych zasadach. Początkowo dane wprowadzane do systemu były niedokładne, co wpływało na jakość raportów. „Czasem klikanie wyglądało tak, jakby robili dla świętego spokoju” – wspomina menedżer produkcji.
Część osób była przekonana, że wdrożenie systemu nie przyniesie wymiernych korzyści, co początkowo utrudniało wprowadzenie nowych rozwiązań.
Różne podejście pracowników (różne charaktery ludzi)
Wśród załogi można było zauważyć cztery grupy:
- Zaciekawieni entuzjaści – szybko załapali, o co chodzi, i od razu chcieli nauczyć się więcej.
- Malkontenci – sceptyczni, otwarcie wyrażający swoje obawy i doszukujący się problemów.
- Neutralni – „klikamy, bo trzeba, ale nie pytajcie nas o szczegóły”.
- Buntownicy – woleli sabotować system, licząc, że ktoś w końcu z niego zrezygnuje.
- Brak obycia z technologią: Starsi pracownicy, którzy nie mieli doświadczenia z komputerami, czuli się zagubieni wobec nowych wymagań. Zdarzały się komentarze w stylu „to nie dla mnie”.
3.2 Adaptacja pracowników: Od niechęci do codzienności
Mimo początkowego oporu proces adaptacji w firmie Tryumf zakończył się sukcesem. Pracownicy, którzy początkowo byli sceptyczni wobec nowego narzędzia, zaczęli dostrzegać jego zalety. Kluczowym elementem było szkolenie pracowników – budowanie świadomości i zaangażowania, które pozwoliło zespołowi zrozumieć, jak system ułatwia codzienną pracę.
Jak wyglądał proces adaptacji?
- Stopniowe wdrażanie: Pierwsze kroki rozpoczęto od testowania systemu na jednej linii produkcyjnej, co pozwoliło na spokojne oswajanie się z nowym rozwiązaniem.
- Tworzenie zespołu wdrożeniowego: W firmie wybrano liderów, którzy szybko zrozumieli działanie systemu i stali się wsparciem dla reszty załogi.
- Współpraca i mentoring: Pracownicy z dłuższym stażem pomagali nowym, tłumacząc podstawy działania systemu i wspierając ich w trudnych momentach. Te osoby, często liderzy zespołów, stały się mentorami dla pozostałych, pomagając im opanować podstawy obsługi systemu.
- Szkolenia pracowników – budowanie świadomości i zaangażowania: Szkolenia zostały zaplanowane w sposób odpowiadający różnorodnym potrzebom pracowników. Zorganizowano praktyczne warsztaty grupowe oraz indywidualne sesje dla osób mających trudności z obsługą technologii, szczególnie starszych pracowników. Liderzy zespołów, przeszkoleni wcześniej, pełnili rolę mentorów, pomagając wdrożyć system na produkcji.
Szkolenia koncentrowały się na praktycznych aspektach systemu, takich jak rejestrowanie czasu pracy czy obsługa panelu pracownika, co pozwoliło szybko opanować najważniejsze funkcje.
- Sukcesywne wdrażanie kolejnych grup pracowników: Proces wdrażania systemu w firmie przebiegał stopniowo, co pozwoliło uniknąć chaosu i zapewniło lepsze przygotowanie zespołu.
Wdrażanie było dostosowane do specyfiki poszczególnych działów, a tempo dostosowywano do ich potrzeb i wyzwań.
Taka metoda pozwoliła nie tylko na płynne wdrażanie systemu, ale też zbudowanie zaufania w zespole, co miało kluczowe znaczenie dla jego dalszego funkcjonowania.
Zalety systemu, które ułatwiły adaptację
- Prosty i intuicyjny interfejs użytkownika: Nawet osoby bez doświadczenia z systemami komputerowymi mogły szybko nauczyć się obsługi systemu.
- Hybrydowa rejestracja produkcji: Możliwość korzystania z tradycyjnych kart pracy obok systemu ułatwiła przejście na nowy sposób działania.
- Logowanie za pomocą RFID: Logowanie do panelu pracownika stało się szybkie i proste, eliminując problemy z pamiętaniem haseł.
- Naliczanie w panelu pracownika przepracowanego czasu: Funkcja ta zwiększyła zaangażowanie, umożliwiając menedżerom śledzenie wyników pracowników.
- NIEOGRANICZONY support: Stałe wsparcie techniczne i merytoryczne zapewniło, że żaden problem nie pozostawał nierozwiązany.
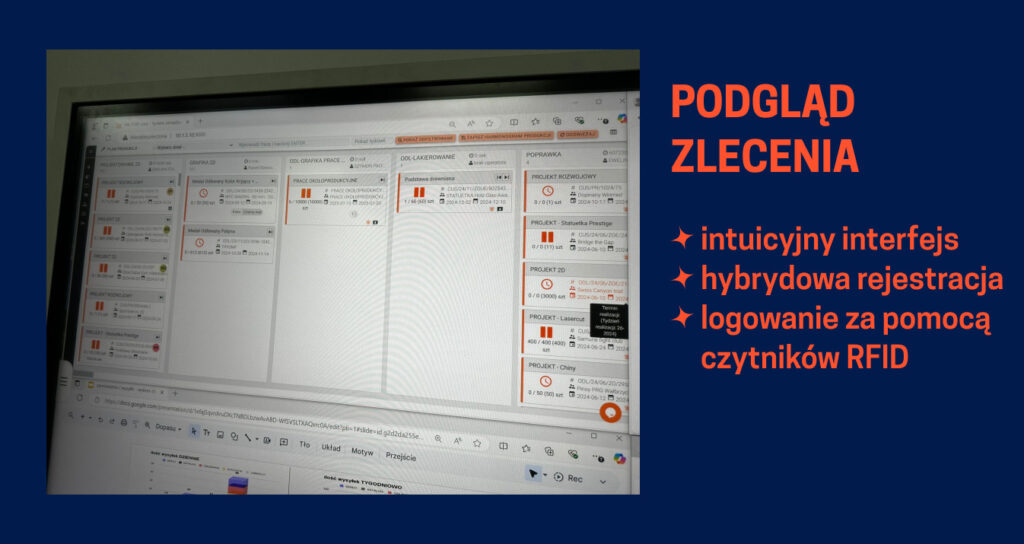
Rozwiązania problemów
Kluczem okazały się jasne zasady i konsekwencja. Gdy pracownicy zobaczyli, że system nie tylko ułatwia planowanie, ale też może pomóc w codziennych zadaniach, zaczęli zmieniać nastawienie. Wprowadzono prostą zasadę: brak dokładności = brak dodatku motywacyjnego. To działało. Ważną rolę odegrał też lider zespołu, który na bieżąco wyjaśniał problemy, kontrolował zaangażowanie pracowników i odpowiadał na pytania.
Zaangażowanie to klucz do sukcesu
Proces adaptacji w firmie Tryumf udowodnił, że tworzenie zespołu wdrożeniowego i konsekwentne budowanie świadomości oraz zaangażowania pracowników to fundament skutecznego wdrożenia. Dzięki temu nowy system nie tylko został zaakceptowany, ale stał się ważnym narzędziem codziennej pracy.
3.3 Pierwsze reakcje pracowników i efekty wprowadzenia systemu
Pierwsze reakcje pracowników na wprowadzenie systemu były mieszane, ale już po kilku tygodniach zaczęły pojawiać się konkretne efekty. Wielu z nich dostrzegło, że nowe narzędzie nie tylko porządkuje codzienną pracę, ale także oszczędza czas. Zamiast ręcznie wypełniać stosy kartek, mogli rejestrować swoje działania bezpośrednio w systemie, co znacząco zmniejszyło liczbę pomyłek.Największym przełomem było wprowadzenie widoku produkcji w czasie rzeczywistym. Kierownicy mogli na bieżąco sprawdzać, na jakim etapie są konkretne zamówienia, a pracownicy widzieli, jakie zadania czekają w kolejce. To usprawniło komunikację i pozwoliło lepiej zarządzać czasem.
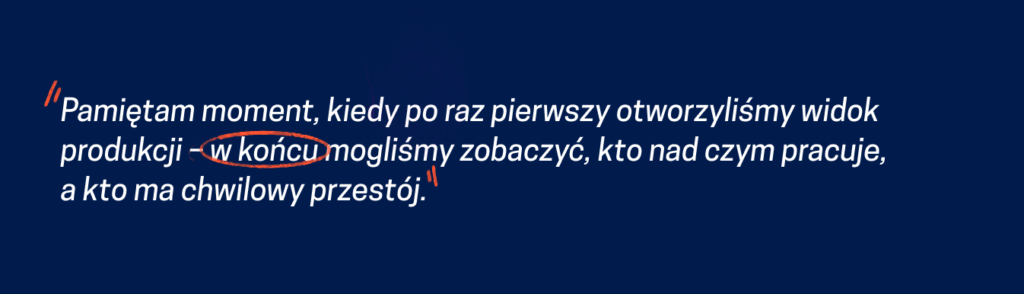
Efekty adaptacji
- Zwiększenie zaangażowania zespołu: Pracownicy zaczęli postrzegać system jako narzędzie wsparcia, a nie kontroli.
- Oszczędności: Wdrożenie systemu przyniosło firmie Tryumf nie tylko usprawnienia w organizacji produkcji, ale także realne oszczędności, takie jak redukcja etatów dzięki automatyzacji procesów.
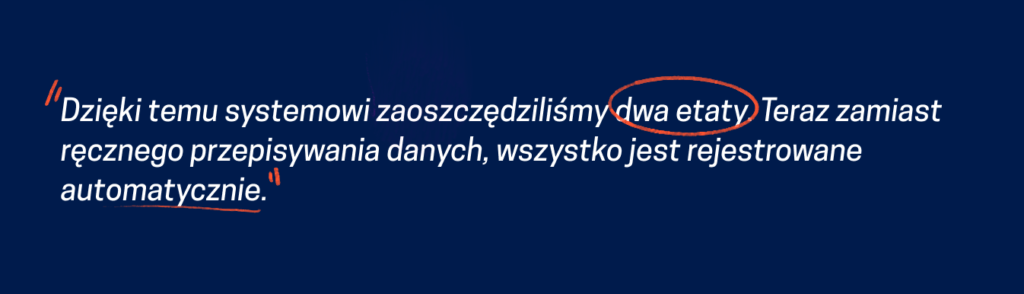
- Lepsza organizacja pracy: Zautomatyzowanie procesów pozwoliło na bardziej precyzyjne monitorowanie produkcji i optymalizację działań.
- Podniesienie jakości danych “klikanie”: System zapewnił dostęp do bardziej szczegółowych i wiarygodnych informacji, co przełożyło się na lepsze decyzje firmy. System zmotywował pracowników do większej dyscypliny. Automatyczne rejestrowanie czasu pracy i zadań sprawiło, że „klikanie” przestało być postrzegane jako dodatkowy obowiązek, a stało się częścią codziennego rytmu pracy.
- Oszczędność czasu: Oszczędność czasu zarówno dla kierownictwa, jak i pracowników.
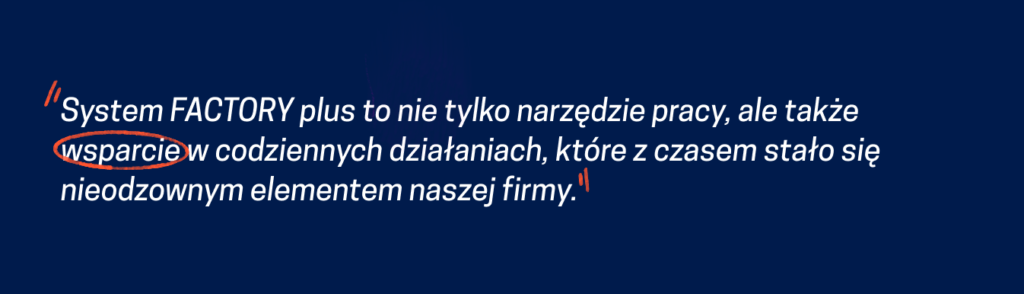
Chcesz, aby Twoi pracownicy z łatwością zaadaptowali się do nowego systemu?
4. Różne perspektywy wdrożenia: Od zarządu po liderów działów
Wdrożenie systemu klasy MES w Tryumfie to nie tylko zmiana systemu, ale też zmiana podejścia do pracy na każdym poziomie organizacji. Od zarządu, przez kierownictwo, aż po liderów działów – każdy miał inne oczekiwania, wyzwania i perspektywę. Ten proces nie obył się bez trudności, ale też przyniósł wymierne efekty, które dziś są odczuwalne w całej firmie. Warto przyjrzeć się, jak wyglądało wdrożenie z punktu widzenia osób, które na co dzień korzystają z systemu.
4.1 Komunikacja z zarządem firmy
Dobra komunikacja była fundamentem całego procesu. Zarząd od początku oczekiwał jasnych informacji o tym, co system zmieni i jakie korzyści przyniesie. Kluczowe było pokazanie, że FACTORY plus to nie tylko technologia, ale narzędzie, które wprowadzi porządek w produkcji i obniży koszty. Regularne raporty o postępach i wyzwaniach pomogły utrzymać wsparcie zarządu na każdym etapie.
4.2 Perspektywa dyrektora produkcji
Dla dyrektora produkcji FACTORY plus miał być odpowiedzią na problemy z brakiem przejrzystości danych. Najważniejszą metryką stała się wydajność – czas operacji, ilość przestojów, czy poziom błędów w produkcji. Dzięki systemowi można było w końcu łatwo monitorować te wskaźniki i podejmować szybkie decyzje.
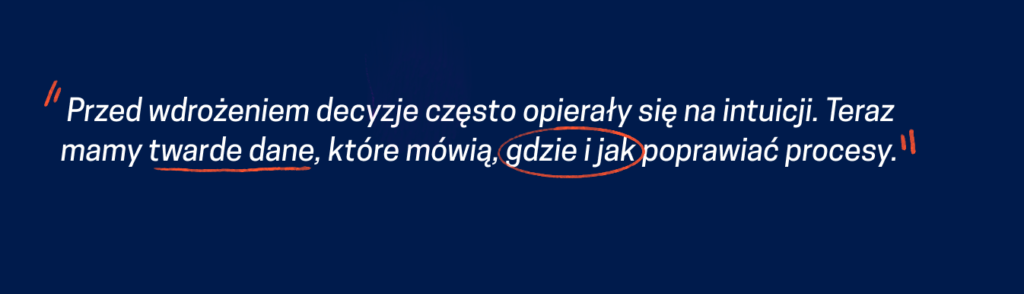
4.3 Wdrożenie z perspektywy kierownika produkcji
- Nadzieje: Dla kierowniczki produkcji wdrożenie FACTORY Plus było jak obietnica porządku. Wierzyła, że system pomoże wreszcie zapanować nad chaosem z dokumentacją i zleceniami.
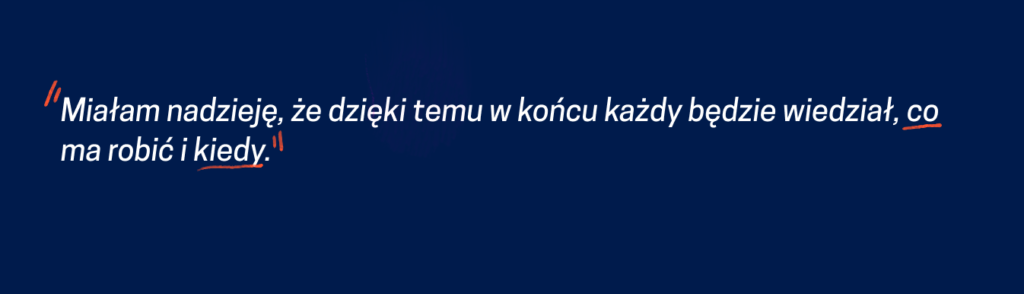
- Trudności: Na początku największym wyzwaniem była zmiana nawyków. Pracownicy, mieli opory przed nauką nowego systemu.
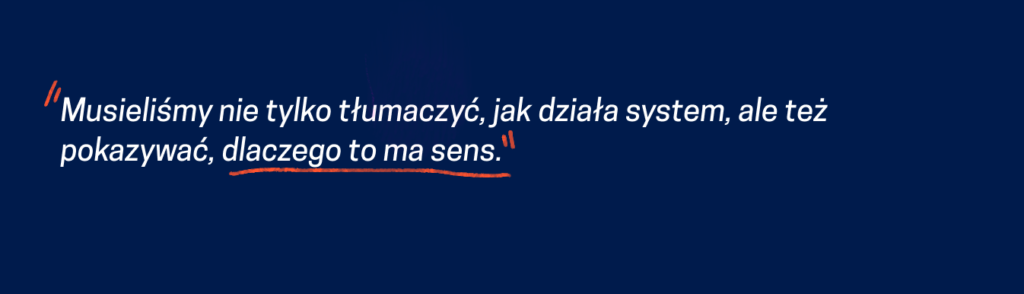
- Współpraca z wdrożeniowcem VISIX: Tutaj kluczowa była elastyczność. Wdrożeniowiec nie tylko dostarczał rozwiązania, ale też słuchał uwag i dostosowywał system do specyfiki Tryumfu.
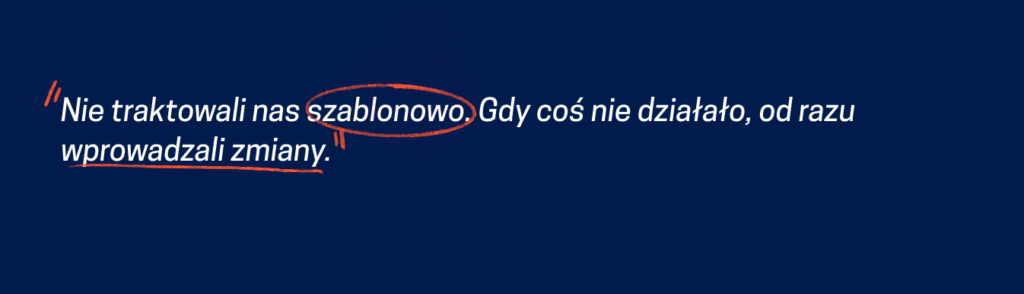
- Uzyskane efekty: Po wdrożeniu widać było konkretne zmiany – mniej chaosu, lepsza kontrola nad kosztami, szybsze decyzje. Kierowniczka podkreślała, że dzięki FACTORY plus praca stała się bardziej przewidywalna, a zespoły działają płynniej.
4.4 Perspektywa liderów działów (brygadziści)
Dla brygadzistów największą korzyścią była przejrzystość – w końcu wszystko mieli w jednym miejscu, a nie na rozrzuconych kartkach. Nie obyło się bez trudności – niektórzy mieli obawy, że system zwiększy nadzór nad ich pracą. Jednak po kilku tygodniach okazało się, że zamiast kontrolować, FACTORY Plus ułatwia codzienne obowiązki.
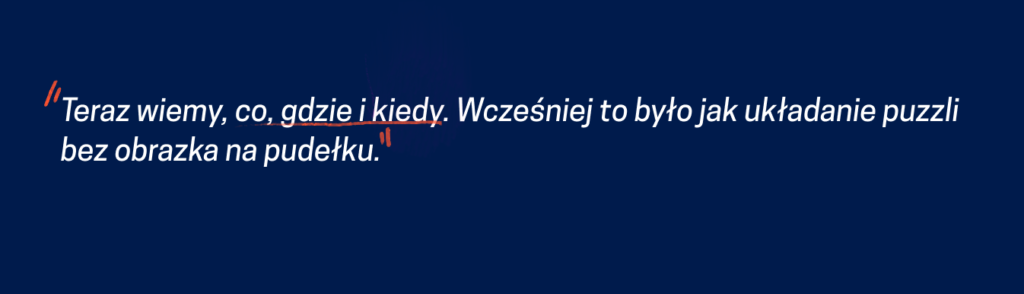
System sprawił też, że liderzy mogli lepiej wspierać swoje zespoły – błędy były szybciej wyłapywane, a planowanie stało się prostsze.
Zrozumienie obaw i potrzeb wszystkich interesariuszy to fundament udanego wdrożenia. W Tryumfie kluczem było zaangażowanie zarówno zarządu, jak i pracowników, którzy mieli realny wpływ na to, jak system będzie działał.
5. Przenoszenie danych produkcyjnych firmy – łatwo, szybko i bez problemów
Wdrożenie nowego systemu to nie tylko nowe funkcjonalności, ale także konieczność zadbania o zgromadzone już dane. W firmie Tryumf kluczowe było zadbanie, żeby wszystkie informacje – bez względu na to, skąd pochodziły – zostały sprawnie zaimportowane i dokładnie przypisane w nowym systemie. Efekt? Dane przeszły migrację bez strat (zgromadzone dane nie zostały zgubione), a firma mogła kontynuować produkcję płynnie i zgodnie z nowymi zasadami.
5.1 Integracja z obecnym systemem – koncepcja
Tryumf już korzystał z systemu ERP, więc integracja z nowym oprogramowaniem była kluczowa. Była to jedna z pierwszych decyzji, które podjęto podczas wdrożenia. Koncepcja zakładała, że system FACTORY Plus będzie synchronizował dane z ERP w czasie rzeczywistym, a import danych do programu miał odbywać się sprawnie i bez błędów, co gwarantowało płynność całego procesu.
5.2 Przygotowanie i wprowadzenie danych do systemu
Przenoszenie danych do nowego systemu zawsze budzi wiele pytań i obaw, ale w firmie Tryumf proces ten został przeprowadzony sprawnie i skutecznie. Dzięki starannej organizacji i etapowemu podejściu, wszystkie dane produkcyjne zostały przeniesione i zorganizowane w nowym systemie FACTORY plus, zapewniając ciągłość pracy i przejrzystość procesów.
Standaryzacja i strukturyzacja danych
W pierwszym kroku firma dokonała standaryzacji nazw oraz struktur danych.
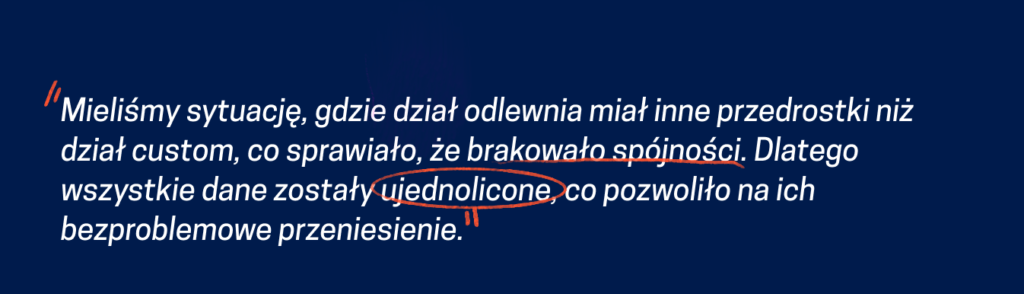
Łatwy import danych do programu
Kluczowym elementem był import danych z Excela i innych programów, w którym przechowywano wiele informacji z poprzedniego systemu. Dane takie jak karty produktów, nazwy operacji czy materiały zostały zaimportowane, co znacząco przyspieszyło proces migracji. Jednakże część danych, takich jak schematy marszrut czy specyfikacje operacyjne, musiały być wprowadzana ręcznie.
Mapowanie danych
Dzięki precyzyjnej analizie struktury danych z poprzedniego systemu, każdy element został dokładnie przypisany do odpowiedniego miejsca w nowym oprogramowaniu.
Synchronizacja danych
Integracja z istniejącym oprogramowaniem ERP zapewniła spójność danych i eliminację ewentualnych błędów.
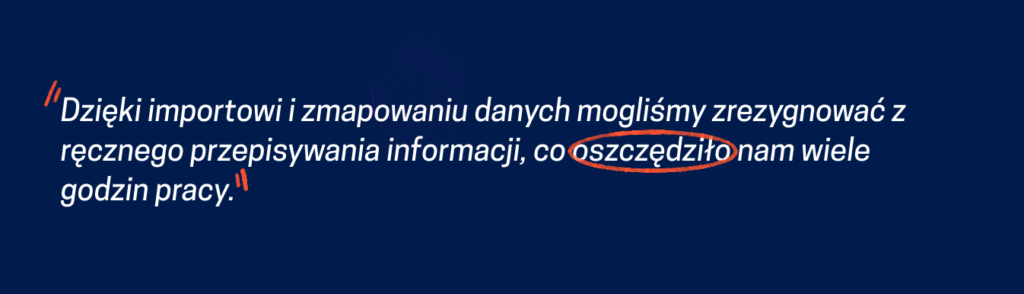
Konfiguracja i dopasowanie
Proces napełniania danych wymagał również dostosowania systemu do specyfiki produkcji firmy Tryumf. Wprowadzono zmiany w strukturze danych, takie jak dodanie narzędzi i materiałów do kart produktów.
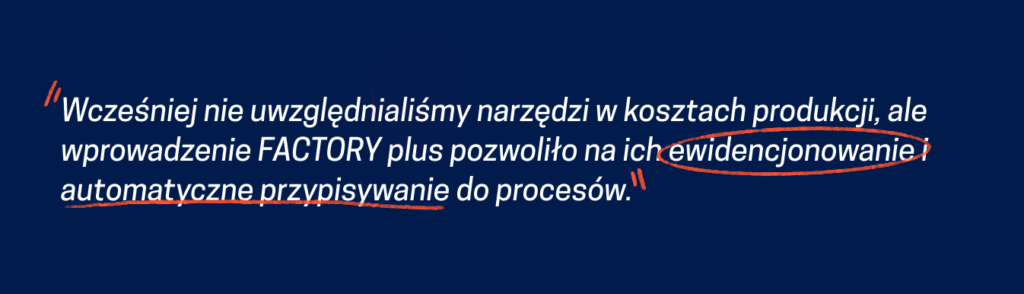
Proces etapowy
Migracja danych z poprzednich systemów odbywała się stopniowo, zaczynając od najprostszych operacji i produktów, takich jak laser cutting, a następnie przechodząc do bardziej skomplikowanych obszarów, takich jak statuetki Prestige. Etapowe podejście pozwoliło na weryfikację poprawności danych na bieżąco i eliminowanie ewentualnych błędów.
5.3 Możliwość instalacji na serwerze lokalnym
Dla firm, które cenią sobie pełną kontrolę nad danymi, system oferuje opcję instalacji na wewnętrznym serwerze lokalnym. Rozwiązanie to:
- Zapewnia niezależność od dostępu do Internetu, co jest kluczowe dla ciągłości pracy w produkcji.
- Pozwala na pełne wykorzystanie zasobów hardware, bez współdzielenia ich z innymi użytkownikami platformy SaaS
- Umożliwia pracę w zamkniętym środowisku, co jest szczególnie ważne w firmach produkcyjnych – precyzyjne dostosowanie do specyfiki firmy, indywidualnych procesów oraz urządzeń produkcyjnych.
5.4 Jak poradziliśmy sobie z integracją z ERP?
W firmie Tryumf kluczowym wyzwaniem było połączenie nowego systemu z istniejącym oprogramowaniem ERP. Dzięki precyzyjnej analizie potrzeb oraz etapowemu podejściu udało się osiągnąć pełną synchronizację danych:
- Rzeczywiste koszty produkcji: Czas operacji i zużycie materiałów były na bieżąco przenoszone między systemami, co pozwalało na dokładne obliczanie kosztów.
- Zautomatyzowanie przepływu danych: Zlecenia produkcyjne były przesyłane między systemami w kilka sekund, eliminując wcześniejsze czasochłonne procesy ręczne.
- Ciągły rozwój: System jest regularnie dostosowywany do zmieniających się potrzeb firmy, co umożliwia dodawanie nowych funkcjonalności, takich jak uwzględnianie narzędzi w kosztach produkcji.
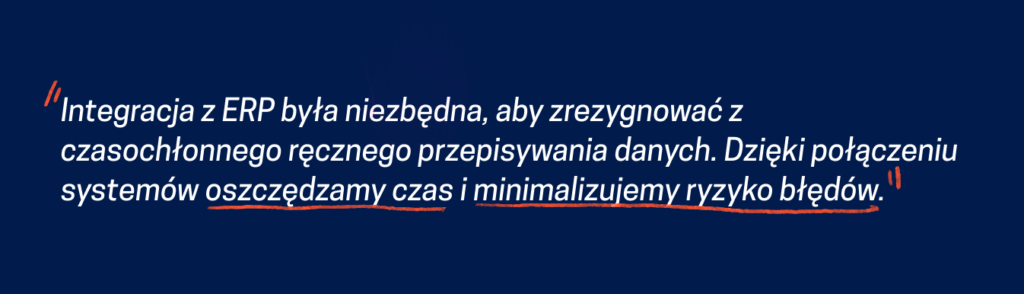
5.5 Kluczowa rola integracji z systemami księgowymi i sprzedażowo-księgowymi
W firmie Tryumf, jednym z priorytetów było zapewnienie pełnej spójności danych pomiędzy nowym systemem produkcyjnym, a istniejącymi rozwiązaniami księgowymi i sprzedażowo-księgowymi. Jak to wyglądało w praktyce?
- Po pierwsze, integracja z programem księgowym pozwoliła na automatyczne przesyłanie danych o kosztach produkcji. Dzięki temu procesy księgowe stały się szybsze, dokładniejsze i wolne od typowych błędów.
- Po drugie, integracja z programem sprzedażowo-księgowym sprawiła, że informacje o stanach magazynowych, zamówieniach i operacjach sprzedażowych przepływały między systemami bez potrzeby ręcznego wpisywania danych.
- Współpraca między systemami to także szybki dostęp do rzeczywistych danych o kosztach produkcji – informacje były aktualizowane w czasie rzeczywistym, co dawało firmie pełną kontrolę nad finansami.
Dzięki tej integracji Tryumf nie tylko uporządkował dane, ale też ułatwił zarządzanie produkcją i sprzedażą. Efekt? Większa przejrzystość, efektywność i możliwość lepszego planowania strategicznego. Wszystko to przy mniejszym wysiłku i większym komforcie codziennej pracy.
Chcesz dowiedzieć się więcej o tym, jak przenieść dane do nowego systemu? Skontaktuj się z nami, a pokażemy Ci, jak łatwo i szybko przeprowadzić migrację danych oraz zapewnić ich pełną integrację z Twoim biznesem!
6. Kontakt z wdrożeniowcem: Klucz do udanej integracji.
Podczas wdrożenia nowego systemu produkcyjnego, kontakt z wdrożeniowcem odgrywa kluczową rolę w zapewnieniu sprawnego przebiegu całego procesu. W firmie Tryumf opieka w czasie wdrożenia była jednym z fundamentów sukcesu, eliminując wszelkie wątpliwości i gwarantując pełne wsparcie po wdrożeniu.
Regularne aktualizacje
Wdrożenie systemu to dopiero początek. W firmie Tryumf wdrożeniowiec zadbał o regularne aktualizacje systemu, co pozwoliło na jego ciągły rozwój i dostosowywanie do zmieniających się potrzeb produkcji. Dzięki temu firma mogła na bieżąco wprowadzać usprawnienia bez przestojów w pracy.
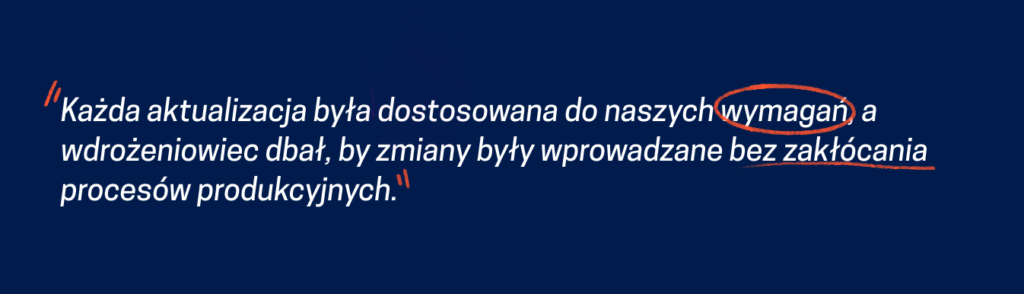
Regularny kontakt i wsparcie
Obawa, że po zakończeniu triala lub wdrożenia zabraknie wsparcia, jest częstym problemem. W firmie Tryumf wdrożeniowiec zapewnił regularny kontakt bezpośredni zarówno w czasie wdrożenia, jak i po jego zakończeniu. Dzięki temu każdy problem, niezależnie od jego skali, był szybko rozwiązywany.
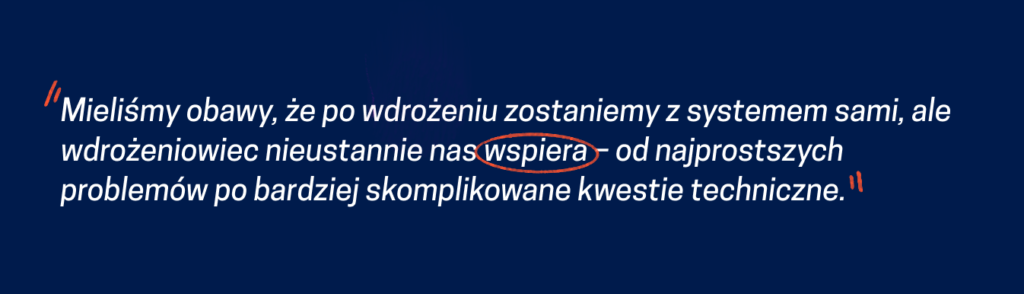
Kontakt z wdrożeniowcem i opieka w czasie wdrożenia są kluczowe dla sukcesu całego procesu. Regularne aktualizacje, możliwość instalacji sprzętu oraz wsparcie po wdrożeniu sprawiają, że firma może z pełnym zaufaniem korzystać z nowego systemu.
7. Zakup i instalacja sprzętu komputerowego
W ramach współpracy firma miała możliwość nie tylko wdrożenia programu do zarządzania produkcją, ale także zakupu i instalacji odpowiedniego sprzętu komputerowego. Dzięki temu każdy etap wdrożenia odbywał się w pełni przygotowanym środowisku, które pozwalało na płynne działanie systemu.
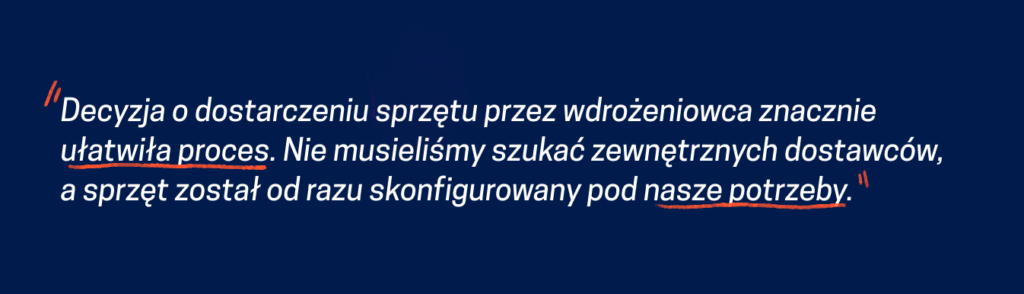
7. 1 Zakup sprzętu komputerowego
W firmie Tryumf wybór komputerów nie był dziełem przypadku, ale efektem przeprowadzonej analizy. Sprzęt musiał sprostać specyficznym warunkom pracy na hali produkcyjnej, gdzie pył, kurz i ograniczona przestrzeń.
Jak przebiega proces wdrożenia programu do zarządzania produkcją, jeśli zaczyna się od zakupu sprzętu? To proste – kluczowe jest dostosowanie urządzeń do środowiska pracy.
Jak wybrano sprzęt?
Przede wszystkim postawiono na niezawodność. Zamiast standardowych komputerów zdecydowano się na laptopy przemysłowe z wytrzymałymi obudowami odpornymi na kurz, pył i uderzenia. Dodatkowo każdy z nich wyposażono w dotykowy ekran, żeby pracownicy mogli obsługiwać system szybciej i wygodniej, bez konieczności używania myszki.
Dlaczego laptopy?
Z dwóch powodów:
- Zajmują mniej miejsca – a tego na hali produkcyjnej zawsze brakuje.
- Są bardziej elastyczne, co ułatwia ich umieszczenie w strategicznych punktach, tak żeby nie przeszkadzały w pracy, a jednocześnie były łatwo dostępne.
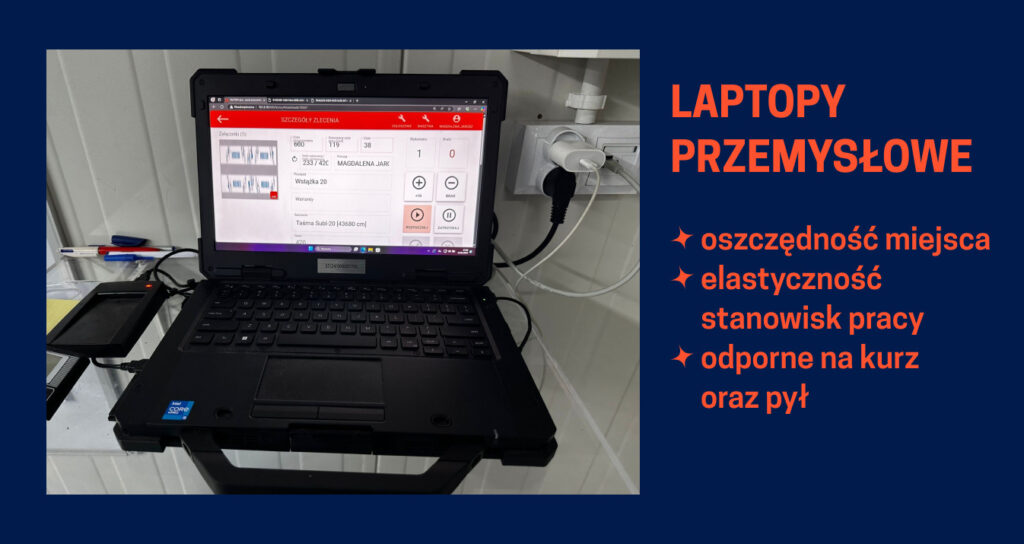
Rozważano jednak inne rozwiązanie – umieszczenie standardowych komputerów w specjalnych obudowach ochronnych, które zabezpieczają urządzenia przed kurzem i pyłem. Ostatecznie jednak uznano, że laptopy przemysłowe, wyposażone w wytrzymałe obudowy i dotykowe ekrany, będą lepszym rozwiązaniem.

Ile komputerów wystarczyło?
Pierwszym krokiem było określenie, ile komputerów naprawdę potrzeba i gdzie powinny być rozmieszczone. Zamiast kupować urządzenie na każde stanowisko, skupiono się na ergonomii. Liczba komputerów została dostosowana do liczby pracowników i częstotliwości korzystania z urządzeń. W efekcie jeden laptop obsługiwał średnio dwa-trzy mniejsze stanowiska, co pozwoliło ograniczyć koszty bez utraty wygody pracy.
W firmie Tryumf inwestycja w odpowiednio dobrane laptopy przemysłowe nie tylko ułatwiła wdrożenie systemu, ale też sprawiła, że codzienna praca stała się prostsza, szybsza i bardziej efektywna.
7.2 Instalacja i konfiguracja sprzętu komputerowego
Wdrożeniowiec FACTORY Plus zadbał o wszystko, co potrzebne do startu – od instalacji komputerów po konfigurację sprzętu.
Cały proces instalacji zajął około tygodnia i obejmował:
- Podłączenie i konfigurację sprzętu,
- przygotowanie infrastruktury sieciowej – zamiast Wi-Fi, które mogłoby być niestabilne w środowisku produkcyjnym, wybrano połączenie LAN,
- konfigurację systemu i dodanie kont użytkowników,
- integracja urządzeń, takich jak czytniki kodów kreskowych.
Czy wdrożenie jest czasochłonne?
Dzięki kompleksowemu podejściu czas instalacji został zminimalizowany do jednego tygodnia, co obejmowało zarówno podłączenie, jak i konfigurację urządzeń. W efekcie sprzęt był gotowy do działania od razu po zakończeniu prac. Dopasowanie sprzętu do specyfiki produkcji pozwoliło uniknąć zbędnych przestojów. Pracownicy szybko docenili intuicyjność dotykowych ekranów i łatwość obsługi.
Co więcej, solidna infrastruktura daje firmie pewność, że system działa niezawodnie i jest gotowy na przyszłe rozszerzenia. Dzięki temu wdrożenie aplikacji nie było tylko jednorazowym działaniem, ale inwestycją w rozwój i przyszłość organizacji.
8. Planowanie, analiza i raportowanie procesów – Twoja firma w liczbach
Wprowadzenie systemu do zarządzania produkcją to nie tylko narzędzie do codziennej pracy, ale również źródło wartościowych danych, które umożliwiają monitorowanie postępów i rozwiązywanie problemów na bieżąco. W firmie Tryumf kluczowym elementem wdrożenia było wykorzystanie modułu raportowania, dzięki któremu firma zyskała lepszą kontrolę nad produkcją, efektywne planowanie oraz możliwość eliminowania strat.
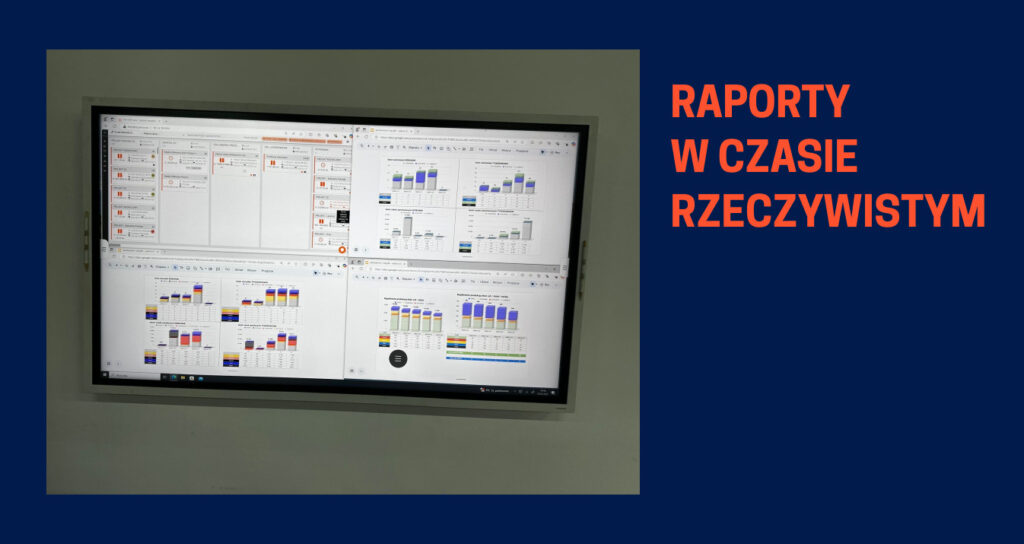
Planowanie budżetu i harmonogramu z precyzyjnymi danymi
Dane generowane przez system wspierają planowanie budżetu i harmonogramu, co pozwala na bardziej precyzyjne zarządzanie zasobami. Raporty w czasie rzeczywistym umożliwiają firmie kontrolę nad kosztami i czasem realizacji zamówień. Na przykład, dzięki analizie danych Tryumf skrócił czas realizacji zamówień, jednocześnie redukując straty materiałowe.
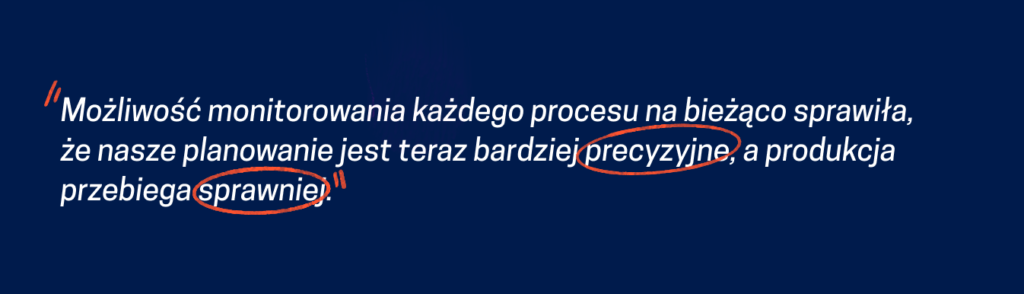
Lepsza kontrola nad produkcją
Największą zaletą systemu jest możliwość generowania raportów w czasie rzeczywistym, które dostarczają informacji o każdym etapie produkcji. Dzięki temu firma może:
- Szybciej reagować na problemy i wprowadzać rozwiązania.
- Identyfikować potencjalne straty i optymalizować procesy.
- Monitorować postępy prac i wydajność zespołu.
- Precyzyjnie planować budżet i harmonogram.
- Testować nowe funkcje dzięki iteracyjnemu podejściu.
Ułatwienie planowania i eliminacja błędów
Choć na początku pojawiła się obawa, że konieczne będzie ręczne przepisywanie produktów, precyzyjne mapowanie danych i system importu informacji znacząco usprawniły ten proces. W rezultacie udało się zgromadzić kompletne dane bez nadmiernego nakładu pracy.

Moduł analizy i raportowania to narzędzie, które wspiera efektywne zarządzanie firmą.
Chcesz zobaczyć, jak analiza i raportowanie może usprawnić procesy w Twojej firmie?
9. Podsumowanie: Efekty wdrożenia systemu do zarządzania produkcją – krok w stronę nowoczesności
Wdrożenie systemu FACTORY Plus w firmie Tryumf okazało się prawdziwą rewolucją w zarządzaniu produkcją. Dzięki kompleksowemu podejściu – od analizy procesów, przez integrację z dotychczasowymi systemami, aż po solidne szkolenie zespołu – firma zyskała nowoczesne narzędzie, które nie tylko ułatwia codzienną pracę, ale też wprowadza nową jakość w organizacji procesów.
Kluczowe efekty wdrożenia systemu:
- Skrócenie czasu realizacji zamówień – Lepsza organizacja pracy oraz precyzyjne dane pozwoliły firmie na efektywniejsze zarządzanie harmonogramami i realizację zamówień w krótszym czasie.
- Redukcja strat materiałowych – Możliwość monitorowania zużycia materiałów w czasie rzeczywistym pomogła zidentyfikować miejsca generujące straty, co przełożyło się na oszczędności.
- Zwiększenie precyzji w planowaniu – Analiza raportów umożliwiła firmie bardziej precyzyjne zarządzanie budżetem, zasobami i harmonogramami, eliminując potencjalne błędy i opóźnienia.
- Lepsza kontrola nad procesami produkcyjnymi – Moduł raportowania pozwolił na śledzenie postępów każdego etapu produkcji, co przełożyło się na szybsze reagowanie na problemy i bieżące usprawnienia.
- Wzrost jakości danych – Dzięki precyzyjnemu rejestrowaniu procesów firma uzyskała bardziej wiarygodne dane, które stały się podstawą do podejmowania lepszych decyzji.
- Optymalizacja wycen produktów – Automatyzacja pozwoliła na szybkie i dokładne generowanie wycen, co wcześniej wymagało czasochłonnych analiz.
- Wzrost zaangażowania pracowników – Dzięki szkoleniom i wsparciu wdrożeniowców zespół zyskał pewność w obsłudze systemu, a intuicyjny interfejs i logowanie RFID ułatwiły codzienną pracę.
- Bezpieczeństwo danych – Migracja danych z poprzednich systemów odbyła się bez żadnych strat, a system jest regularnie aktualizowany, co pozwala na ciągły rozwój i dostosowywanie do potrzeb firmy.
- Integracja z programami ERP – Synchronizacja danych między systemami zapewniła spójność informacji i automatyzację procesów, eliminując konieczność czasochłonnego przepisywania danych.
- Zwiększona przejrzystość procesów produkcyjnych – Liderzy działów i menedżerowie zyskali możliwość monitorowania produkcji w czasie rzeczywistym, co poprawiło komunikację i kontrolę nad realizacją zleceń.
- Zmniejszenie chaosu w zarządzaniu danymi – Standaryzacja i integracja z poprzednimi systemami wyeliminowały problemy z niespójną danych, co usprawniło codzienną pracę.
- Oszczędność czasu administracyjnego – Eliminacja ręcznego wprowadzania danych pozwoliła na zaoszczędzenie wielu godzin pracy.
- Wsparcie dla procesów rozwojowych – Regularne aktualizacje i możliwość dostosowywania systemu do nowych potrzeb pozwalają firmie dynamicznie reagować na zmieniające się warunki rynkowe i wymagania klientów.
Usprawnienie zarządzania metrykami:
- Czas operacji – System pozwolił na dokładne monitorowanie czasu pracy poszczególnych operacji, co wcześniej było szacowane lub uśrednianie.
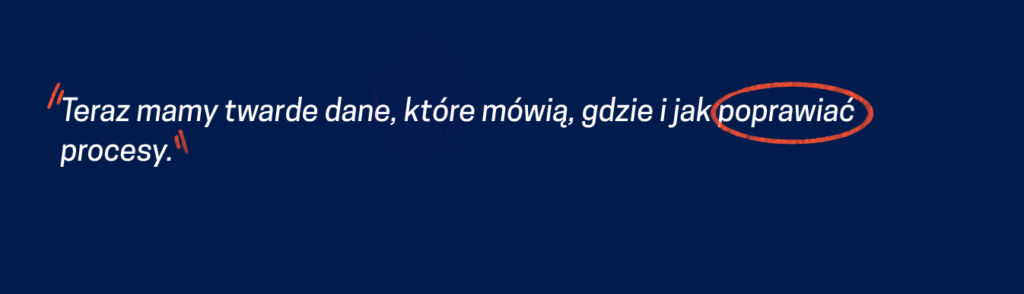
- Ilość przestojów – Dzięki systemowi można śledzić, gdzie i dlaczego występują przestoje, co umożliwiło szybsze reagowanie.
- Poziom błędów w produkcji – Rejestracja danych w systemie umożliwia wychwytywanie nieścisłości, takich jak błędy w zamówieniach czy niezgodności w procesach.
- Koszty produkcji – System umożliwił precyzyjne obliczanie kosztów na podstawie zużycia materiałów i czasu operacji.
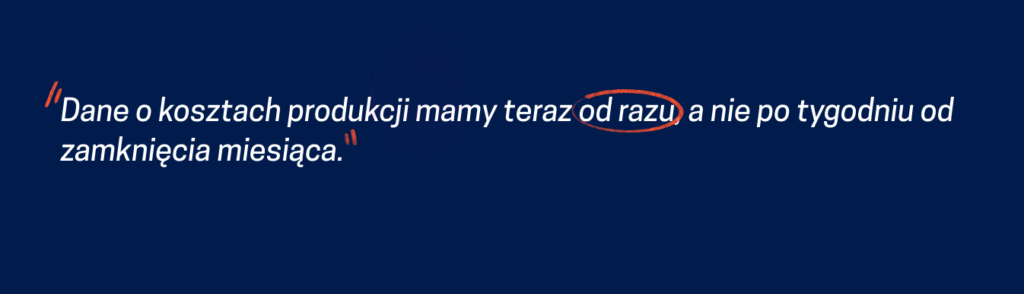
- Wydajność zespołu – Panel pracownika i logowanie RFID pozwoliły bieżąco rejestrować czas pracy oraz wyniki pracowników.
Wprowadzenie FACTORY plus to przykład, jak efektywne wdrożenie systemu może odmienić funkcjonowanie firmy. Tryumf zyskał nie tylko nowoczesne narzędzie do zarządzania produkcją, ale również stabilny fundament do dalszego rozwoju. Dzięki zaangażowaniu zespołu wdrożeniowego, regularnym aktualizacjom oraz współpracy z dostawcą oprogramowania, firma osiągnęła nowe standardy efektywności i precyzji.