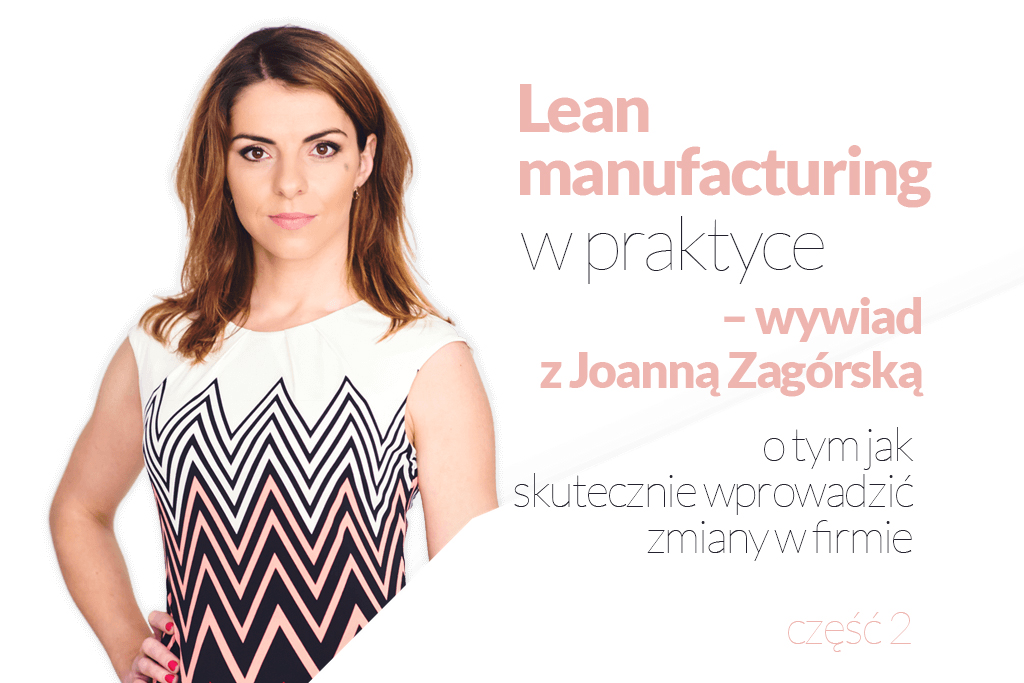
W pierwszej części wywiadu ekspertka od wprowadzania strategii zgodnych z lean manufacturing Joanna Zagórska opowiedziała czym jest lean manufacturing oraz z jakimi problemami borykają się przedsiębiorcy, którzy decydują się na wprowadzenie go do firmy. W tej części wywiadu znajdują się przykłady firm, w których lean manufacturing już funkcjonuje, a co najważniejsze dla firm, które jeszcze takiego systemu nie mają – co zrobić, żeby rozpocząć skuteczne wdrażanie zmian w sposobie zarządzania swoją firmą. Wkroczenie w XXI wiek najczęściej kojarzy się z nowoczesną technologią. Ale żeby mogła ona zagościć w przedsiębiorstwie potrzebny jest pomysł i zaangażowanie. Odpowiedź na to kto i w jakim stopniu powinien to zrobić, a przede wszystkim jak? – znajduje się poniżej.
- Na blogu opisałaś wizytę w fabryce BMW w Berlinie. Powiedziałaś, że produkcja jest zgodna z lean manufacturing. Co takiego tam zobaczyłaś?
To była fabryka motocykli. Połączyłam ją ze swoją prywatną pasją. W każdej grupie, w każdym kraju, w którym prowadziłam projekty organizowałam wycieczkę do różnych fabryk. Poza BMW byliśmy w Mercedesie na Węgrzech, w Audi i w Volkswagenie na Słowacji i w TPCA, czyli Toyota, Peugeot, Citroen Automobile w Czechach. Ponieważ ci ludzie pracowali w usługach, chciałam, żeby zobaczyli lean manufacturing w rzeczywistości i przede wszystkim to co było widać w fabrykach to spokój. Nie ma chaosu, wszystko dzieje się wg określonego porządku. Fabryki są bardzo wizualne. Ludzie są podzieleni na zespoły. Bardzo często widać kto należy do jakiego zespołu ze względu na zróżnicowane kolory roboczego ubrania.
Ale to co najbardziej widać to prezesów, czy dyrektorów w GEMBA, czyli na produkcji. Gdy jechaliśmy pociągiem przez fabrykę, to przewodnik powiedział, że jedna z osób, które mijaliśmy to dyrektor operacyjny, który stał i obserwował proces. To było podstawowym przykładem na to, że fabryka działa zgodnie z lean manufacturing. Wszędzie było widać monitory, na nich dane w wizualny sposób prezentujące ile już zostało wykonane z dzisiejszego planu pracy. Jeśli pracownik mieścił się w polu zielonym, pracował zgodnie z dzisiejszą normą, a jeśli pojawiało się pole czerwone był już poza nią. Nie dowiadują się tego na koniec dnia, tylko w bieżącym momencie. Wtedy można szybciej reagować. Jeśli jest jakiś problem, to od razu zatrzymują całą linię. Nie produkują więcej defektów. Mają światełka, żeby zawołać kierownika. Nie boją się sygnalizować i mówić o problemach.
- Co na to pracownicy? Kiedy pojawia się problem szczebel kierowniczy wie, że trzeba coś zrobić, zatem chce zmian. A co na to pracownicy? Jak reagują?
Bardzo często strachem i oporem, głównie wynikającym z nieznajomości tej metodologii. Niestety lean manufacturing często kojarzy się ze zwolnieniami, z przykręcaniem śruby. Więc wszystko zależy tak naprawdę od tego, czy pomysł został dobrze zakomunikowany ludziom. Ale i tak strach przed zmianami mamy wszyscy wpisany w DNA i boimy się ich trochę. Pierwsze prace z ludźmi polegają na tym, żeby ich do takich zmian przekonać. Trzeba zacząć od małych kroków, tak zwanych QuickWinów, czyli rzeczy, które mogą im pomóc lepiej pracować, żeby zobaczyli, że te zmiany są naprawdę dla nich. Chodzi tu na przykład o naprawienie kołyszącego się krzesła, powieszenie kotarki, bez której panie siedzące przy drzwiach często się przeziębiały.
To na początek. A później wyciąganie pewnych informacji od pracowników dotyczących pewnych czynności, które ich zdaniem są bez sensu. Bo tu nie chodzi o to, żeby pracowników do czegoś zmuszać. Wtedy kiedy sami mają tą decyzyjność i biorą odpowiedzialność za swoje procesy, to chętniej chcą je zmieniać, bo widzą, że ktoś im nie pokazuje palcem, tylko od nich te informacje wyciąga i ich słucha.
- Lean manufacturing to m. in. ciągłe udoskonalanie siebie i procesów. Niektórzy pracownicy boją się, że narzuci im ono nieustanne podnoszenie poprzeczki. Będą musieli zatem robić coraz więcej w tym samym czasie, albo nawet coraz szybciej. A przecież tak to nie działa, prawda?
Opowiem anegdotę z firmy produkcyjnej. Miałam usprawnić linię, na której pracowało 10 pań lutujących różne elementy do mierników elektrycznych. Były strasznie sfrustrowane, nigdy nie umiały wyrobić normy, a szefostwo cały czas podkręcało im śrubę. Mimo, że bardzo „zasuwały”, ich proces był tak rozregulowany, że nie były w stanie wykonać normy. Wówczas na ogół uważa się, że jest za mało ludzi. Jak widać, niekoniecznie.
Na początku mojej współpracy z paniami, wytłumaczyłam dlaczego chcę zmierzyć ich tempo oraz jak możemy usprawnić proces ich pracy. Po moich pierwszych pomiarach wiedziałam już, że da się to wszystko usprawnić w taki sposób, żeby częstotliwość wypuszczania gotowego produktu z linii była zgodna z wymaganiem klienta. Pierwszą reakcją był opór, jak to zwykle bywa. Na wiadomość, że będę mierzyć tempo ich pracy niektóre przyspieszały, bo się bały, że jak okaże się, że za wolno pracują, to zostaną zwolnione, inne zwalniały, bo się bały, że jak będą za szybko pracować, to im się jeszcze bardziej podkręci śrubę.
No więc narysowałam im jak wyglądają ich stanowiska i ile powinno być czynności na każdym stanowisku, żeby norma została osiągnięta w czasie. Zaczęłam też pytać je co im najbardziej przeszkadza na linii. Między stanowiskami zgromadzonych było bardzo dużo półprduktów, co powodowało nieporządek i niepotrzebny chaos, jednej zacinała się lutownica, druga miała rozchybotane krzesło, więc codziennie rano wszystkie wbiegały na halę, zajmowały inne miejsca, żeby tylko na nim nie siedzieć. To są rzeczy, które naprawdę uprzykrzają codzienną pracę.
Zaczęłam więc powoli wszystkie te trudności rozwiązywać. Wówczas zobaczyły, że otwierając się na wprowadzane przeze mnie zmiany też coś z tego mają. Następnie zaczęłyśmy analizować czynności, które wykonywały w taki sposób, żeby każda miała mniej więcej tyle samo do zrobienia. Okazało się w końcu, że tempo wypracowane przez te panie było dość szybkie i nie chciały go zmieniać, ponieważ podczas nocnych zmian mogłyby zasypiać. Pracowały zatem sprawnie, ale czasu miały na tyle, żeby napić się wody, czy zamienić dwa słowa z koleżanką. Bo praca nie może być tak całkiem automatyczna. Dla usprawnienia została naprawiona dodatkowa taśma, żeby pracownice nie musiały same przynosić półproduktów.
Po pierwszym teście nowych ustawień zapytałam panie jak im się pracowało, bo założona norma została wykonana. Jedna z pań powiedziała, że pierwszy raz wychodzi z pracy taka wypoczęta. To stwierdzenie było dla mnie największym sukcesem. Bo nie chodzi tylko o dane, wypracowaną normę, czy poprawiony czas. Chodzi o to, że pracownice zaangażowały się w proces wprowadzania zmiany i zauważyły, że praca w nowym porządku jest lepsza.
To nie jest podkręcenie śruby. Tylko takiego zmienionego, ulepszonego procesu trzeba pilnować. Kiedy opracowywałam proces na innej linii w tym samym przedsiębiorstwie i przechodziłam koło tych pań ze swoim stoperkiem, to jedna z nich zawołała mnie, żebym ponownie ją zmierzyła, bo czuła się niezsynchronizowana z pozostałymi pracowniczkami linii. Są wytyczne, żeby przynajmniej raz w tygodniu mieć taką sesję usprawniającą, bo zawsze są jakieś problemy. Jak to w Toyocie mówią „No problem is a problem”. Jeśli ktoś nie widzi problemów nie ma jak się usprawniać i poprawiać.
- Gdzie widzisz oszczędności po wprowadzeniu strategii lean manufacturing? – Czas? Pieniądze? Rotacja? Oszczędność zasobów? Gdzie je widać, jak je proponujesz wykorzystać?
Wszędzie. Zaczynając od produkcji na pewno znikają przestoje i defekty, czyli poprawia się jakość. Oszczędności widać również w polityce zarządzania zapasami. Robiłam taki projekt w Anglii, gdzie zaoszczędziłam prawie 2 mln. funtów, przez to, że przejrzeliśmy cały magazyn i dostosowaliśmy całą politykę zapasową do tego co naprawdę powinno być w magazynie. Okazało się, że nie było w nim wielu potrzebnych rzeczy, natomiast zamrożono sporo gotówki w produktach zupełnie niepotrzebnie zgromadzonych w magazynie. Dzięki lepszej komunikacji i lepiej rozplanowanym zadaniom jest lepsza kultura pracy i spada rotacja, bo w takiej firmie każdy chce pracować. Jeśli człowiek budzi się z myślą, że znowu musi iść „do roboty”, to pewnie tam długo nie zostanie.
- “We are what we repeatedly do. Excellence, then, is not an act, but habit.” (Jesteśmy tym co powtarzamy. Doskonałość to nie jednorazowa czynność, ale nawyk) ~Arystoteles
Jak sprawić, by ten ciągły ruch był motywujący, a nie stresujący dla pracowników?
To zależy jaki jest system w firmie. Jeśli jest zgodny z lean manufacturing, to ciągle jest czas na poprawę, na sesje usprawniające, na mówienie o problemach. Chodzi też o to, żeby ciągle były jakieś cele, ale nie za wielkie. Bardzo popularnym hasłem jest KAIZEN, czyli tzw. dobra zmiana z j. japońskiego. Chodzi o małe kroki, żeby nie zaczynać od wielkich rewolucji i nie dawać ludziom wielkich celów na wyrost. Chodzi o drobne zmiany, żeby codziennie coś poprawić. Z tych małych ciągłych kroczków robią się potem wielkie oszczędności i wielkie osiągnięcia.
- Wszędzie jest jakiś haczyk. Gdzie zwykle pojawiają się minusy po wdrożeniu innowacji?
Jeśli chodzi o kierownictwo, to muszą odpuścić kontrolę. Muszą przekazać ją pracownikom, a nie zawsze jest to łatwe, bo skoro szef jest szefem, to uważa, że on wie najlepiej. Bardzo często są to przeszkody ambicjonalne, schowane gdzieś w mentalności.
Druga rzecz to trwanie w kulturze lean manufacturing, czyli audyty i standardy powinny być wpasowane w DNA całej firmy.
- “Tell me and I will forget, show me and I may remember, involve me and I’ll understand.” (Powiedz mi a zapomnę, pokaż a może zapamiętam, zaangażuj – zrozumiem) – jaka jest rola pracodawcy w budowaniu lean manufacturing. Niektórzy relacje rozumieją jako organizowanie raz w roku wyjazdu integracyjnego. A to nie o to chodzi, prawda?
Zacznijmy od odwróconej piramidy. Tradycyjnie szef był na górze i pokazywał palcem niższym szczeblom. Na dole natomiast byli ci biedni ludzie, którzy produkują i dostarczają wartość, bo to przecież dzięki ich pracy cała firma czerpie – oni mieli się najgorzej. Chodzi o to, żeby odwrócić tę piramidę, żeby szef był wspierający na dole, a ludzie pracujący nad wartością na samej górze, ponieważ dzięki nim cała firma zarabia. Zatem tak naprawdę cała firma powinna ich wspierać.
- Jak zatem powinien zachować się pracodawca, który chce zacząć wprowadzać zmiany w swojej firmie i chce odwrócić tę piramidę?
Z pewnością powinien zacząć od zadawania pytań swoim pracownikom i słuchania co ludzie mają tak naprawdę do powiedzenia. Nie powinien bagatelizować zgłaszanych problemów, a najlepiej jeśli będzie je obserwować w „GEMBA”, czyli wśród ludzi na produkcji. Tam najwyraźniej widać zachodzące procesy i można najskuteczniej planować ich usprawnianie. Wtedy ludziom będzie się lepiej pracowało. Pracodawca powinien się przekształcić raczej w obserwatora, albo wręcz coach’a.
- Jakie są korzyści dla obu stron w firmie?
- Co zyskuje pracodawca, a co traci?
Przez zoptymalizowanie zapasów oszczędza pieniądze. Także dzięki właściwemu ustawieniu procesów poprawia jakość produkcji i minimalizuje straty. Traci natomiast kontrolę i część czasu jaki trzeba poświęcić na udoskonalanie. - Co zyskuje pracownik, a co traci?
Z pewnością lepszą atmosferę w pracy, ponieważ komunikacja jest lepsza, lepsze są procesy i ergonomia pracy. Chodzi też o to, żeby pracownicy mieli stanowiska lepiej dostosowane do swojej pracy. Mniej nadgodzin, ponieważ jeśli się wszystko dobrze poukłada i dobrze określi cele, to można wszystko zmieścić w czasie. Mniej stresu. Natomiast jeśli przejmie odpowiedzialność za swoją pracę i procesy, to traci możliwość narzekania na szefostwo.
- Najtrudniej jest znaleźć przedsiębiorcom czas na wdrożenie innowacyjności. Jak mają go znaleźć? Wyłączyć się z pracy na pół roku? Pracować po godzinach i w weekendy? Wielu już to robi, by nadążyć z realizacjami. Co w tej sytuacji?
Jeśli nic nie zrobi, to będzie tylko gorzej. Jeśli firma rośnie, to problemy też rosną. Trzeba zacząć od znalezienia jednej godziny w tygodniu. Każdy problem rozwiązany podczas tej jednej godziny będzie generował więcej czasu i spokoju w przyszłości. Zatem zacząć od małych kroków. Na pewno się nie da wyłączyć na pół roku. Przecież firma musi działać i zarabiać. Można po pierwsze zbudować zespół z kilku pracowników, którzy by się zajmowali lean manufacturing. Być może na początku z pomocą konsultanta, a później już po szkoleniach i warsztatach wybrani pracownicy mogliby już sami „odkopywać” zaistniałe problemy organizacyjne w firmie. Ważne też, żeby przyjrzeć się gdzie są prawdziwe przyczyny tej sytuacji. Bo może to są nieodpowiednie zlecenia, albo jest ich za dużo? Często przedsiębiorcy zastanawiają się dlaczego ludzie nie nadążają, a przecież powinni. Wtedy pojawia się tzw. backoffice, czyli ludzie poprawiają błędy i często tracą na to nawet połowę czasu.
Jeśli jest chaos, to warto zacząć nawet od jednej godziny, później od szkoleń i od wygospodarowania czasu dla tej ekipy, która będzie mogła powoli usprawniać proces, w innym przypadku, jeśli się zaniecha działań, energia włożona w pierwsze próby zostanie zmarnowana. Trzeba ją zainwestować i regularnie ponawiać próby aż do skutku. Trzeba być wytrwałym. Wtedy osiągnie się sukces.
Bardzo dziękuję za wszystkie porady i podzielenie się swoimi doświadczeniami związanymi z wprowadzaniem lean manufacturing.
Dziękuję.
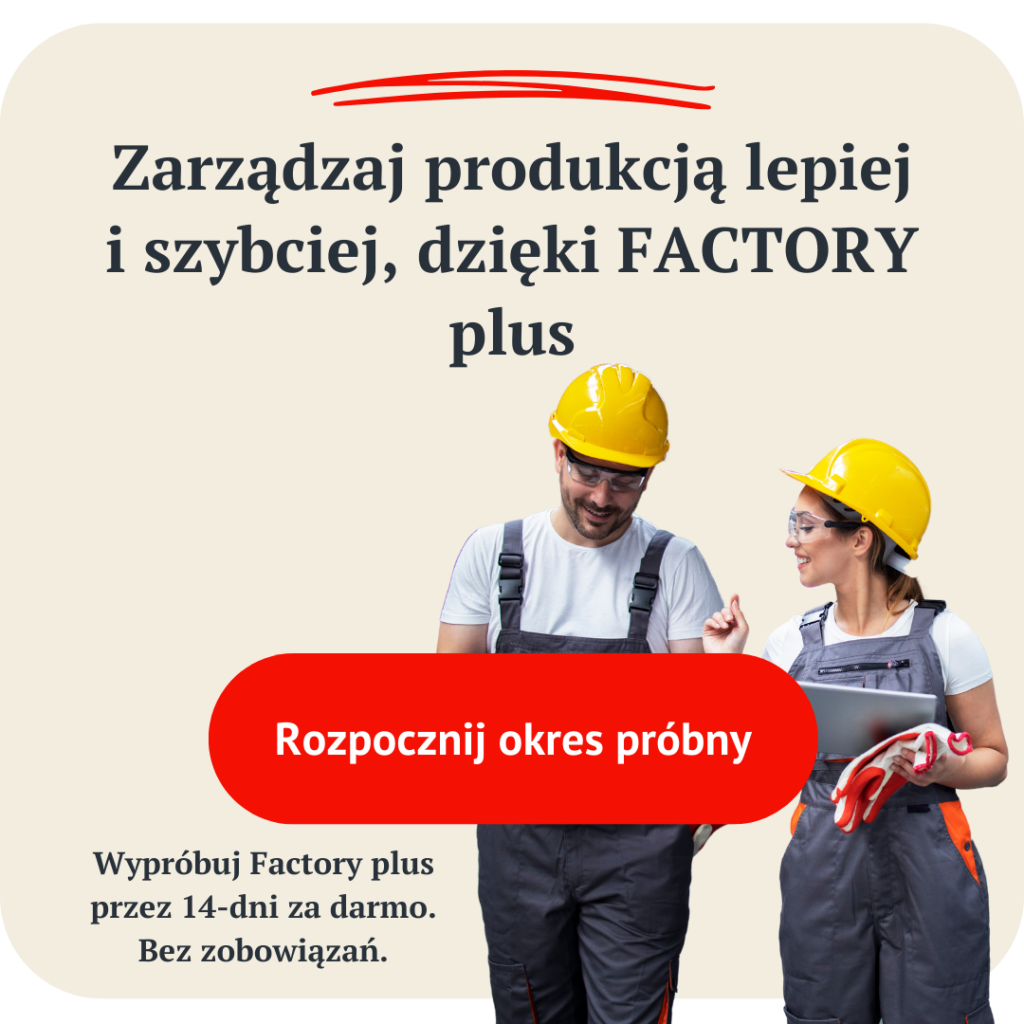